This publication is intended for a wide audience that includes poultry producers, service persons, ventilation industry personnel, Extension personnel, and researchers.
Thermal Stratification
Unlike mature birds, chicks and poults cannot maintain their body temperature because they do not produce enough body heat, nor can they regulate heat loss or gain. Therefore, they require supplemental heating; for example, day-of-hatch chicks require air temperatures at least 88°F, but broilers six weeks or older are comfortable at air temperatures lower than 70°F. During brooding or cool weather, lower ventilation rates are required. Reduced air mixing due to lower ventilation rates combined with supplemental heating causes the lighter warm air to rise to the ceiling with the cooler air staying near the floor. The difference between the ceiling and floor temperature is thermal (or temperature) stratification (Figure 1). This can lead to the birds feeling cold or the heaters running longer, increasing energy use. In litter-based houses that are inadequately sealed (leaky), inadequately ventilated, or have leaky drinkers, cooler floors can lead to wet litter. As will be discussed later, wet litter affects bird health and welfare, and drying litter could be more important than mitigating thermal stratification only.
Sole reliance on inlets and cold weather ventilation rates to control stratification in poultry houses can lead to the ceiling being as much as 20°F warmer than the floor (Czarick and Lacy, 2000). In cool or cold weather, higher ceiling temperature can increase building heat loss. Although ceiling heat loss data for US broiler houses could not be located, ceiling heat loss accounted for 25% of the total heat loss from a three-story 19,500-bird broiler house in Canada (Cordeau and Barrington, 2010). Typically, thermal stratification, and hence, heat loss is higher in open ceiling houses that have less insulation in the ceiling than houses with drop ceilings. Forced air furnaces that heat the air instead of the floor cause greater thermal stratification (Figure 1) than other heaters. Because pancake brooders provide some radiant heat, thermal stratification is lower (9°F) (Bottcher et al., 1988) versus forced air furnaces. Compared to pancake brooders, thermal stratification will be lower with radiant brooders and particularly with infrared tube heaters.
Mixing fans installed near the ceiling of the poultry house can mix the air to reduce or even eliminate thermal stratification. In Figure 2(a), with the mixing fans off, thermal stratification was 5.2°F versus 3.4°F with the fans on. Higher ceiling and floor temperatures in Figure 2 (a) versus Figure 2 (b) were likely due to cycling of the infrared heater.
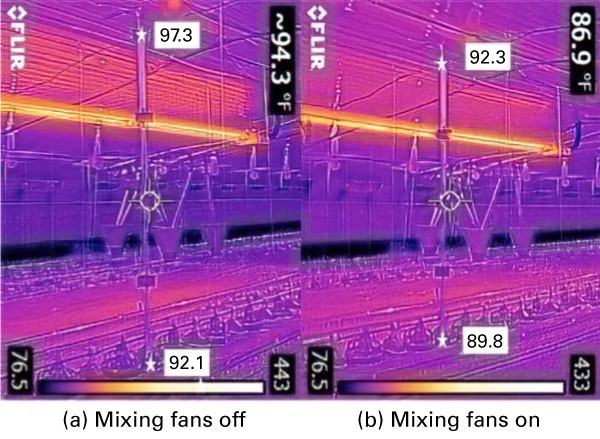
Figure 2. Thermal stratification in a broiler house with tube heaters with (a) mixing fans off and (b) mixing fans on. Temperature (°F) measurements were made on black aluminum strips just above the litter and just below the ceiling. Note the high temperature at the drop ceiling above the tube heater.
Horizontal vs. Vertical Mixing and Types of Mixing Fans
Mixing fans, also called stir fans or circulation fans, reduce thermal stratification by mixing the air, horizontally or vertically. Horizontal mixing fans push the air along the ceiling (parallel to the long side of the house) with each successive fan moving the air further, causing the air to warm up (Figure 3). As the air travels along the ceiling, it draws in air from below, promoting mixing. The air then travels down the brood curtain or end wall to the floor where it transfers the heat to the young birds. The number of fans pushing air in either direction will depend on the length and width of the house. Fans placed too close to the end wall or brood curtain may create high air speeds that could chill the chicks, but this will depend on the air speed, house temperature, and age of birds.
Examples of horizontal mixing fans are shown in Figure 4. The basket fan (Figure 4(a)) ranges in size from 14 inches to 24 inches, is the least expensive, and consumes the least power; some basket fans are variable speed. The panel fan (Figure 4(b)), ranges in size from 12 inches to 24 inches. Unlike the basket fan, the panel fan has an orifice that generates a compact discharge pattern with higher velocity forcing the air to travel farther down the ceiling, promoting better air mixing. The box fan (Figure 4(c)), available in sizes up to 48 inches, is a panel fan with a frame that can allow it to be used as an exhaust fan. Because larger box fans can cause chilling, they are not used as mixing fans, except in open ceiling houses. The strings or cables attached to the bottoms of the panel and box fans (Figure 4) can be used to change the angle of the fans or increase ground clearance for equipment travel. Slanting the mixing fans slightly toward the ceiling will cause the air to attach to the ceiling and travel farther, improving mixing. Mixing fans angled downward toward the floor can chill young birds.
In vertical air mixing (Figure 5), air is moved from the floor to the ceiling in the updraft mode (Figure 5(a)) or ceiling to the floor in the downdraft mode (Figure 5(b)). In the downdraft mode, high airspeed at the floor level at moderate temperatures can chill young birds. At an air temperature of 85°F, floor airspeed of 100 feet per minute caused chick body temperature to drop by less than 0.5°F during the first week but not at 90°F. At 95°F, chick body temperature was unaffected even at 200 feet per minute (Lu, 2019). Hence, young birds are less likely to be chilled when vertical mixing fans are operated in the updraft mode, but air temperature should be considered.
Some vertical mixing fans are shown in Figure 6. Paddle (or ceiling) fans (Figure 6(a)) reduced total energy use by 8% and eliminated thermal stratification in broiler houses (Flood et al., 1998). Bottcher et al. (1988) reported that 56-inch paddle fans reduced temperature stratification by up to 27.4°F with higher fan speeds being more effective. Paddle fans are economical and move large amounts of air; further, they are variable speed and some fans can be operated either in the downdraft or updraft mode. For best performance, the blades should be reversed on their fan mounts for updraft operation instead of reversing motor direction (Boon and Battams, 1988), as is common practice. Inadequate clearance limits their use in houses with drop ceilings.
Figure 6(b) shows Vostermans Ventilation’s Vertical V-FloFan; other manufacturers also make similar fans. As the air is pulled up by the fan (Figure 6(b)), the shroud at the top guides it toward the sloped house ceiling; the attached air then travels along the ceiling and down the sidewalls before reaching the floor.
Chore-Time manufactures an air destratifier, the Cubo S/R (Figure 7) that pulls warm air from the ceiling and distributes it above the floor with a blower. The destratifier is also available with a built-in heater.
Performance data for many mixing fans are available at the University of Illinois’s Bioenvironmental Structural Systems (BESS) Laboratory website at no cost. BESS Labs lists basket fans under circulation fans and provides information on airflow rate (cubic feet per minute), centerline velocity (feet per minute) at five fan diameters, and ventilation efficiency ratio (VER) (cubic feet per minute per watt). Because box fans are also used for ventilation, they are tested for airflow rate and VER at static pressures up to 0.3-inch water column, but not velocity, unlike basket fans. BESS Labs always tests box fans with shutters, and in many cases with cones. Because mixing fans are never used with cones or shutters, airflow rates without the accessories must be obtained from the manufacturer.
Impact of Air Mixing Rate and Fan Type on Thermal Stratification, Litter Quality, and Footpad Health
Czarick and Lacy (2000) compared energy use in two broiler houses with forced air furnaces, one with two horizontal 18-inch mixing fans in the brood chamber and the other with no mixing fans. Over three weeks, the house with the mixing fans used 30% less propane, had a warmer floor (by 5°F), and drier litter than the house without the mixing fans. In the study by Czarick and Lacy (2000), the mixing fans ran only when the furnaces ran. Running mixing fans continuously is more effective in reducing thermal stratification (Czarick, 2006a).
Mou (2020) reported that birds in a broiler house with lower air movement (15% mixing fan capacity with basket fans) had more footpad lesions at different time points and more severe lesions beginning on day 14 than the house with higher air movement (30% mixing fan capacity with panel fans). Mou (2020) did not report on thermal stratification. We calculated the mixing capacities based on the number and airflow rates of the fans, as well as the house floor dimensions provided by Mou (2020) and an assumed height of 9.5 feet.
Czarick et al. (2023) compared eight Cubo S/R vertical mixing fans (3,410 cubic feet per minute, (Figure 7) with eight 24-inch horizontal mixing fans (6,500 cubic feet per minute) in two identical 40-foot × 500-foot broiler houses. The Cubo S/R released air 18 inches above the floor and created air movement in a radius of 15−20 feet. With a mixing fan capacity of 15%, vertical air mixing reduced temperature stratification to less than 5°F, while with a 30% mixing fan capacity, horizontal air mixing reduced it to less than 2°F. Horizontal mixing produced airspeeds in the range of 100–150 feet per minute over most of the floor and led to more uniform litter temperatures than vertical mixing. Horizontal mixings did not adversely affect the chicks, generally led to drier litter, and better footpad quality.
Hence, acceptable thermal destratification in broiler houses can be achieved using a mixing fan capacity, on a per-minute basis, equal to 10–15% of the brood chamber volume. But 15% mixing capacity is inadequate for improving litter quality. Based on several field studies, Czarick (2023) recommended a minimum mixing capacity of 20% to improve litter (and hence, footpad) quality. This is especially true for houses with built-up litter, for the winter flocks, when litter and footpad concerns are the highest (Mou, 2020). For example, for a mixing rate of 20% (per minute) for a brood chamber measuring 250 feet × 40 feet × 9.5 feet, a mixing fan capacity of 19,000 cubic feet per minute would be required. To provide 19,000 cubic feet per minute, three 24-inch panel fans, each moving 6,500 cubic feet per minute in free air (Czarick, 2023), would be required. In winter, inadequately sealed houses could require more air mixing. Because higher mixing capacities can create excessive floor-level airspeeds, chicks must be watched for signs of discomfort. In warmer weather, with increased ventilation, air mixing can be reduced.
In addition to the mixing fan capacity, the fan type is important. Shah et al. (2022) compared thermal stratification in two identical broiler houses with forced air furnaces for one week starting at chick placement. One house had a mixing capacity of 51% provided by seven 18-inch basket fans, while the other had a mixing capacity of 13% provided by two 18-inch panel fans (covered with burlap filters). (The experimental burlap filter, coated with citric acid, was evaluated for its ability to trap ammonia.) For the first five days (Figure 8), both houses had an identical thermal stratification of 0.9°F. The panel fan’s airflow rate decreased as the filters became clogged with dust, but daily manual cleaning mostly restored airflow for the first five days. But during the last two days (weekend), when the filters were not cleaned, thermal stratification increased (Figure 8). Hence, during the first five days, probably due to superior air mixing, the two panel fans provided the same level of destratification as the seven basket fans despite having about a quarter of the airflow rate.
After deciding on the mixing fan capacity, the type and number of fans must be selected. This will govern their spacing. Because there are many different types (and sizes) of mixing fans, poultry houses, and brooding management practices, recommendations cannot be provided for each situation. Some spacing recommendations are provided by Czarick (2006 a, b; 2023) and Campbell et al. (2016), (for open ceiling houses), though the older references are based on lower air mixing. Some broad recommendations and general comments are summarized below.
Broad Recommendations
-
Only agricultural fans approved for use in high humidity and moisture conditions must be used as mixing fans in poultry houses.
-
Mixing fans should be run continuously while the house is in the heating stage.
-
Although mixing fan airflow rate (per minute) equal to 10–15% of brood chamber or house volume can control thermal stratification, at least 20% mixing fan capacity is required to maintain dry litter in winter. Higher mixing fan capacities may be required for leaky houses that use forced air furnaces.
-
The manufacturer’s recommendation should be considered in deciding fan spacing. Recommendations for European poultry houses may not apply to US poultry houses due to differences in size (particularly, height) and management. In North Carolina, North Carolina Cooperative Extension can assist with fan spacing.
-
Paddle fans may be feasible only in open-ceiling houses, with the updraft mode preferred to avoid chilling young birds. For effective thermal destratification, one 60-inch paddle fan or two 36-inch fans per 40-foot length of house up to 49 feet wide will suffice (Boon and Battams, 1988). For wider houses, two 60-inch fans per 40-foot length of house will be required.
-
In a brood chamber 40 feet or less in width, a single row of horizontal or vertical mixing fans is sufficient. Half of the horizontal mixing fans should blow air toward one end wall or brood curtain and the other half of the fans should blow air in the opposite direction. In the off-end, all the mixing fans should blow air toward the exhaust fans and away from the brood curtain. In whole-house brooding, half of the fans should move air in one direction and the other half in the other direction. See Campbell et al. (2016) for additional details.
-
In a brood chamber 54 feet or wider, two rows of horizontal or vertical mixing fans are required. The two rows of horizontal mixing fans should move air in opposite directions. In the off-end, both rows of horizontal mixing fans should move the air toward the exhaust fans. For houses 66 feet or wider, angling the fans inward at 45° improves mixing (Campbell et al., 2016).
-
Horizontal mixing fans can be spaced 20−70 feet apart (Czarick and Lacy, 2000). Spacing will depend on fan specifications, mixing capacity required, and house or brood chamber dimensions. Manufacturers may use different sizes of motors on the same size fan; therefore, airflow rates and velocities should be considered.
-
Vertical fan spacing will be based on its airflow, house dimensions, and mixing capacity required. Using the Multifan V-FloFan (~3,000 cubic feet per minute) as an example, for a 250-foot × 40-foot × 9.5-foot brood chamber and a mixing capacity of 20%, six to seven fans would be required.
-
Fans with wire guards spaced close together (Figure 6(b)) can clog faster and decrease airflow rates during operation compared to those with guards spaced farther apart (Figure 4(a)).
-
Although panel fans are more expensive than basket fans, they provide better air mixing, leading to drier litter. With fewer panel fans, maintenance will be lower than with more basket fans.
-
Placing the mixing fan in line with the tube heater will reduce the heater’s effectiveness in heating the floor. The fan should be placed to the side and angled slightly up, toward the ceiling, to capture the heat rejected by the shroud, to be transported to the floor.
In summary, proper selection of mixing fans, with respect to type, capacity, and location, can reduce energy use and improve thermal comfort, litter quality, and footpad quality. Higher air mixing capacities are required to achieve good litter quality than are required for thermal stratification. Further research using computer modeling could be used to evaluate the impact of fan type, spacing, and location on thermal stratification and litter quality.
References
Boon, C. R., and V. A. Battams. 1988. “Air Mixing Fans in a Broiler Building—Their Use and Efficiency.” Journal of Agricultural Engineering Research, 39 (2), 137–47. ↲
Bottcher, R. W., G. R. Baughman, and L. B. Driggers. 1988. “Temperature Stratification in Broiler Houses and the Effects of Ceiling Fans.” Applied Engineering in Agriculture 4 (1): 66–71. ↲
Campbell, J., D. Brothers, J. Davis, J. Donald, and G. Simpson. 2016. “Benefits of Recirculating Fan Systems.” Poultry Engineering, Economics, and Management Newsletter (90, January). National Poultry Technology Center, Auburn University. ↲
Cordeau, S., and S. Barrington. 2010. “Heat Balance for Two Commercial Broiler Barns with Solar Preheated Ventilation Air.” Biosystems Engineering 107 (3): 232–41. ↲
Czarick, M. 2006a. “1/15 Hp Circulation Fan Update.” Poultry Housing Tips 18 (2). University of Georgia Cooperative Extension Service. ↲
Czarick, M. 2006b. “Circulation Fans for Open Ceiling Houses.” Poultry Housing Tips 18 (10). University of Georgia Cooperative Extension Service. ↲
Czarick, M. 2023. “Basic Circulation Fan System Design.” Poultry Housing Tips 35 (2). University of Georgia Cooperative Extension Service. ↲
Czarick, M., and M. P. Lacy. 2000. “Reducing Temperature Stratification in Houses with Forced Air Furnace.” Poultry Housing Tips 12 (4). University of Georgia Cooperative Extension Service. ↲
Czarick, M., C. Mou, and B. Fairchild. 2023. “Vertical vs. Horizontal Circulation Fan Systems.” Poultry Housing Tips 35 (4). University of Georgia Cooperative Extension Service. ↲
Flood, Jr., C. A., J. L. Koon, R. D. Trumbull, and R. N. Brewer. 1998. “Energy Savings with Ceiling Fans in Broiler Houses.” Applied Engineering in Agriculture 14 (3): 305–09. ↲
Lu, T. L. 2019. “Effect of Air Movement on Chick Body Temperature During Brooding.” Master's thesis, University of Georgia. ↲
Mou, C. 2020. “Litter Management Strategies in a Commercial Broiler House.” PhD diss., University of Georgia. ↲
Shah, S. B., K. Earnest, E. O. Oviedo-Rondón, P. Kolar, and I. Singletary. 2022. “Simultaneous Reduction of Thermal Stratification and Ammonia Concentrations in Poultry House During Brooding and in Cool Weather.” Applied Engineering in Agriculture 38 (2): 375–86. ↲
Publication date: Jan. 15, 2025
AG-974
N.C. Cooperative Extension prohibits discrimination and harassment regardless of age, color, disability, family and marital status, gender identity, national origin, political beliefs, race, religion, sex (including pregnancy), sexual orientation and veteran status.