The environmental impacts of processes or activities are growing concerns as the global implications of these impacts are observed. Although carbon equivalents are considered to be a major factor in climate change, other emissions (air, water, and soil) can have major environmental and human health implications locally, regionally, and globally. Life cycle assessment (LCA) methodology is a quantitative procedure to evaluate environmental impacts related to emissions within a set system boundary, commonly including climate change as a category. Many groups are using LCA-derived data and models to drive business and policy decisions. This publication reviews the methodology behind LCA and describes an example analysis for grain production from maize.
Life Cycle Assessment Background
An LCA can be employed for carbon accounting and used to evaluate other critical environmental impacts, such as acidification, ozone depletion, eutrophication, smog, and human health effects (Table 1). A related publication, AG-793 Carbon Accounting: Description and Methodology, reviews the intricacies of global climate change and carbon accounting. The LCA process is similar to carbon accounting, except it can be used to evaluate a larger number of emissions and impact factors using a life cycle approach. The guiding principles of an LCA follow the International Organization for Standardization (ISO) standards ISO 14040 (ISO, 2006a) and ISO 14044 (ISO, 2006b). These two ISO standards provide an overview of the steps of an LCA: (1) Goal and Scope Definition; (2) Life Cycle Inventory Analysis; (3) Life Cycle Impact Assessment; and (4) Interpretation.
Life Cycle Assessment Process
This section will present an overview of the LCA procedure. For further guidance, consult ISO 14040 (ISO, 2006a) and ISO 14044 (ISO, 2006b). While proper preparation is imperative to conducting an LCA, experience is incredibly important. The interpretation phase, however, allows for further modifications throughout the analysis.
Goal and Scope Definition
The goal and scope definition provides structure for the analysis to ensure uniformity. The study’s goals need to include the rationale for conducting the LCA, the intended audience, and whether results are to be publically disclosed. The project scope of an LCA is the planning stage with areas of determination such as system boundary, functional unit/allocation, data requirements/quality, and report format/need for critical review. Other aspects of the goal and scope definition are outlined in the corresponding ISO standards (ISO, 2006a; ISO, 2006b). A well-defined goal and scope definition will assist later in the analysis when the sheer immensity of calculations seems staggering.
Setting a proper system boundary is arguably the most critical aspect of the goal and scope definition and, possibly, the entire LCA process. Fundamentally, this is a process model with the system boundary dictating what will and will not be analyzed in the system. A process model is a conceptual model of a system broken down into process units (e.g., harvest) and appropriate flows between units (e.g., fuel, lubricant, and product move to subsequent operations). It is impractical to analyze all aspects of a system because of the complexity of minute details, such as equipment production specifics, and the circuitous nature of the analysis (e.g., petroleum fuels are utilized to transport petroleum fuels). This circular pattern of many indirect emissions requires an allocation procedure to be established at the start of the analysis.
Depending on system specifics, the boundary can be modified considerably while staying within the LCA framework. The boundary will be affected by the goals of the analysis and whether or not the results will be used for comparative analysis. It is possible to focus only on direct impacts, such as those coming from the facility, and ignore indirect impacts, such as those from upstream and downstream processes. Direct impacts are compiled from both point sources (e.g., a sewage pipe running into a stream), some of which have existing monitoring guidelines, and non-point sources (e.g., runoff across a field into a stream), which can be difficult to assess. When evaluating indirect impacts, one method is to quantify inputs and outputs from the system, then use either information from vendors or standardized data from an inventory database. Focusing only on direct emissions, and disregarding the entire life cycle, is only appropriate in limited circumstances and requires proper reporting.
Use of a consistent functional unit (e.g., kilograms of product generated) provides a reference to ensure data uniformity. The significance of this practice is related to the allocation procedure, especially when multiple products are produced from a single system. It is preferable to differentiate by product production pathway; however, this differentiation is not always possible, and it requires an allocation procedure. If the functional unit encompasses the entire system—a farm for example—an allocation procedure is not needed; yet, complications arise when comparisons between different size operations and changes in co-product production occur. Selection of an allocation procedure can significantly influence results and requires documentation.
Determining data requirements and quality constraints is important. These requirements and constraints may constitute the use of annual average values or evaluating specific instances of highly monitored events and the difference between using database values versus monitored emissions (discrete or continuous). The choice between publicly accessible data and proprietary information is tied to the audience defined for the LCA. In this light, internal business information may not be appropriate for publicly disclosed results, and average national data may not be suitable for internal reviews.
Preparing for properly formatted documentation and determining the need for a critical review will expedite the production of the final version of an LCA. Properly formatting the report can legitimize the analysis and reduce time required for tedious modifications. Depending on the goal, use of a third party for conducting the LCA may be preferable to reduce the risk of bias; otherwise, a critical review by a third party may be advisable.
Life Cycle Inventory Analysis
Compiling a life cycle inventory begins the process of assigning emission values to operations within the boundary of the system in question. Calculations will differ depending on the source of data values, whether actual monitored data or an inventory database of average values is utilized. Determination of inventory values will also depend on whether the system currently exists or is conceptual. Allocating process flows in a uniform fashion is critical with most industrial operations producing multiple products. It may be necessary to redefine the system boundary during this step, which is typical, but modifications need to be noted in the analysis. This need for redefining the boundary may arise from data constraints (quality, consistency, or availability), revised goals or scope, or any other reasonable rationale with proper reporting. Calculations can also include infrastructure emission values (e.g., lime production for concrete) and indirect emissions (e.g., emissions from coal mining for electricity production) depending on the defined boundary. Many studies create an inventory with the average emissions from unit operations, but it is also possible to look at seasonal variations or focus on worst-case scenarios.
Joliet et al. (2003), TRACI (2013)
Life Cycle Impacts Assessment
After compiling the life cycle inventory, an appropriate set of impact factors are applied for impact aggregation. Two primary categories of life cycle impact factors exist: mid-point and end-point. Mid-point assessment methods are more scientifically verifiable (Bare et al., 2000) and use a set standard of impact category for a given inventory value, such as methane to carbon dioxide (CO2) equivalents. The use of end-point impacts strives to give an actual economic or environmental outcome to the emissions. Although end-point assessment methods are well formulated, they generally apply a number of assumptions that deviate from measureable outcomes, such as an increase in mean global temperature due to methane emissions. During this step, it is possible to specifically categorize (e.g., human health), spatially normalize (e.g., regionally or nationally), or weight the impacts to determine a total LCA score. Use of these standardization techniques is optional, will depend on the goal of the specific study, and may incorporate additional uncertainty into the analysis.
There are multiple environmental and human health impacts associated with emissions, making it difficult to determine the correct impact categories associated with the system being assessed. A host of categories exist for related mid- and end-points. Although it does not encompass all possibilities, Table 1 outlines some common impact factors.
Non-point source emissions and some impact categories may be difficult to quantify. Accounting for land use (m2), water use (L), waste disposal (kg), fossil fuel depletion (MJ), and mineral depletion (kg) may be straightforward, but determining the impacts associated with each of these categories is not. Differentiating these emission values into distinct categories can better account for the associated impacts (e.g., arable vs. marginal land, tap vs. well water, and municipal vs. chemical waste). Some published general values exist for non-point sources, but these can vary greatly depending on differences in the characteristics and properties of the source. For example, emissions from wastewater treatment lagoons can be influenced by geographic location, influent, design, and many other factors. In this regard, using generalized data for non-point sources can be problematic. The temporal and spatial characteristics of an emission can also influence outcomes. For example, land use change from bioenergy production on a plot scale in the short term may not repay the carbon stocks (Manomet, 2010), but long-term observation (Lucier, 2010) shows the biogenic nature of this energy source. The choice of impact factors included in an LCA analysis can affect the results significantly.
During the impact assessment phase, spatial and temporal effects that can modify the actual impacts of the analysis should be taken into account. This is not a concern with mid-point impacts since the emissions are standardized with regards to a uniform emission standard, with no actual environmental outcome being determined. Where those emissions take place, whether they are point or non-point sources, and whether specific thresholds are met to cause impacts are all important factors when evaluating results. Variations in time of emission can also affect actual impacts. Consider whether the emissions are continual or intermittent and whether the time of the year or day has an effect.
Life Cycle Interpretation
The interpretation portion of the analysis occurs continually throughout the LCA process. Interpretation is the systematic process of determining conclusions by identifying significant issues, evaluating how well the data was compiled, and compiling findings and recommendations within the guidelines of the goals and scope. Despite the standardized structure of the LCA framework, it is incredibly flexible in supporting a wide range of goals and scopes.
Conducting a Life Cycle Assessment
A life cycle assessment can seem like a daunting task because of the complexity of the many systems we find interest in, especially with expanding system boundary size. It is important to adequately prepare during the goal and scope step, but be prepared for modifications as the analysis progresses, as is permissible through interpretation. The previously outlined basic methodology can fit a wide range of systems, with industry, residential, government, academic, and commercial groups having successfully used LCA methodology for both actual and conceptual systems. This type of analysis is commonly utilized for the comparison of system options whether for research, system modifications, or construction.
The most prominent LCA software packages are Gabi (GaBi, 2013) and SimaPro (SimaPro, 2013). These programs are user-friendly impact calculators with various databases containing equipment information, GHG inventories for standard operations, and sets of impact factors. Process flows are constructed by the user, and data can be modified by user preference. Depending on specific system knowledge, modifications may not be advisable since database values are referenced and changes may alter the integrity of the calculations. Publicly available software, such as the Greenhouse Gases, Regulated Emissions, and Energy Use in Transportation Model (GREET, 2013), are useful but can contain embedded assumptions that need to be understood, or modified, to accurately model specified systems. Other methodologies, such as the Economic Input-Output Life Cycle Assessment (EIOLCA, 2013), are modified from the basic LCA framework but may be sufficient depending upon goals and scope.
Though these programs can assist with the process, they are not mandatory for developing an LCA. Following standard methodology, proper accounting, and thorough record keeping/ reporting will ensure the legitimacy of the analysis. Process information is available through various sources, including process engineering software such as ASPEN (AspenTech, 2013), and values can also be obtained from many government and research institution sources, many of which are freely accessible. Inventory databases are also available from commercial sources, such as Ecoinvent (Ecoinvent, 2013), and publically available sources, such as the US Life Cycle Inventory Database (US LCI, 2013). Specific process inventories are available from various organizational entities, such as Glass for Europe (Usbeck et al., 2011) and the American Chemistry Council (ACC, 2011). Impact databases are also available from commercial and public sources, such as the Tool for the Reduction and Assessment of Chemical and other Environmental Impacts (TRACI, 2013) and IMPACT 2002+ (Jolliet et al., 2003).
There are many other publicly and commercially available resources for conducting an LCA, but it is important to ensure that proper sources are utilized for the system to accomplish specified goals.
It is common for some energy analysis publications to use the phrases life cycle energy analysis, LCA energy, life cycle energy audit, or similar statements. These analyses follow the basic outline of an LCA but focus on energy as the major metric of interest, not accounting for the environmental impacts mentioned in Table 1 and many others. Many LCA publications calculate energy values, and some also compare these to economic evaluations of their specific system of interest. Energy calculations are sometimes referred to as energy audits and economic evaluations may be termed technoeconomic evaluations, or some variation of these.
A basic understanding of how these studies are conducted is imperative to determine how applicable the results are to a specific system. LCA calculations are made with specific parameters and production scenarios in mind, and the results do not always apply when the system operations and impacts are modified. The true strength of an LCA is the total accounting of environmental impacts related to a specific system to determine areas for process improvements, create baseline data, or compare system alternatives.
LCA Process Example: Grain Production From Maize
Corn grain production in North Carolina was chosen as an example system for practical application of the LCA methodology. With different system boundaries and input values, final impact values could have been significantly modified. The example discussed here can be used as a basic framework and was designed to represent minimum-till corn grain production in eastern North Carolina. It is important to note that production systems can change with factors such as soil type, management strategies, annual/seasonal weather patterns, available equipment, location, previous land use, and other associated factors.
Goal and Scope Definition
Goal
The goal of the study was to serve as an example of how the LCA analysis procedure can be used to determine environmental impacts (example impacts shown in Table 1), specifically in relation to the production of corn grain (maize) in eastern North Carolina. This analysis was developed for public use as an example for individuals interested in the LCA methodology.
Scope
Table 2 outlines various parameters related to the scope of the analysis. Most thorough, professionally conducted LCA analyses follow some specified reporting format with a significant amount of boilerplate included.
The specific system of interest was production of corn grain in eastern North Carolina with a functional unit of one bushel (56 pounds). This system followed the growth cycle of corn, accounting for associated inputs and use of a single iteration method for indirect emission sources (detailed in the Life Cycle Inventory Analysis section).
A system boundary was set around all farm operations terminating at grain elevator delivery (Figure 1). A minimum-tillage crop management strategy was employed with relatively high grain yields for eastern North Carolina (160 bushels per acre). Acquisition of raw materials and processing data were included from publicly accessible sources.
A number of processes were not selected for inclusion in the system boundary: land use change (direct and indirect), equipment manufacture, seed production, and storage losses. The study excluded land use changes from the system boundary due to the inconsistency of land use change metrics; however, it did account for arable land. Since continual agricultural use of the field was assumed, land use change may be accounted for as zero. Equipment manufacture was not included because of the lack of specific publicly available data. Generalized sets of raw material inputs for equipment manufacture are available, such as Heller et al. (2003), but inconsistencies existed between manufacturing operations and specific equipment. Seed production was not accounted for due to the lack of knowledge of seed stock production techniques, which is commonly genetically modified in the United States. Storage losses were assumed to be zero, resulting from proper grain drying and limited storage time. Decomposition, however, can cause additional environmental impacts, especially from high moisture grain. Changes in soil carbon stock and resulting emissions were not included because a minimum-tillage strategy was used to maintain or increase soil carbon. Finally, agrochemical runoff and volatilization were not considered in this analysis because of the site-specific nature of these parameters. If specific information were available on chemical fate-transport with detailed site information, runoff and volatilization may be an important parameter to include.
Acquisition, manufacture, and use of raw materials were included within the system boundary (Figure 2). Impacts of agrochemicals (herbicides) and potassium were determined from energy use values only. Agrochemicals were evaluated this way because of the proprietary nature of their production, making publicly available data scarce. Although they were not outlined in Figure 2, raw material process flows within the electricity boundary included energy production and use from coal, nuclear, fuel oil, and biomass.
This simplified example system had only a single material considered as an output (corn grain), so an allocation procedure was not required. It was possible to consider some additional products, such as corn cobs and stover, at the farm. These residues have been proposed for use in bioenergy production, and there are some niche markets available, such as animal bedding and feed, that may have been incorporated in the system, if warranted. For this LCA, the residues were not part of the system described.
A mid-point assessment approach was utilized to determine impacts for this LCA analysis. The US Environmental Protection Agency’s (EPA) Tool for the Reduction and Assessment of Chemical and Other Environmental Impacts (TRACI) was chosen as a publicly available database normalized for the United States. Though the TRACI database consists of a wide range of impact categories, only select impacts (Table 3) were used in this analysis. No additional normalization, grouping, or weighting took place.
For the interpretation section, the results of this simplified LCA were compared with other analyses of corn grain production systems. The comparison was difficult because other studies had varied results from differences in system boundary, inputs, and all other aspects of the analysis. Other aspects of interpretation took place throughout the LCA analysis to update and modify values as warranted.
A data quality requirement was established for using the best publicly available data to allow for ease in duplication of results, which is not as straightforward when using proprietary data. Data inputs focused on values from North Carolina, followed by the southeastern United States, the entire United States, and finally, global averages. A major weakness of using publicly available data as a data source is the need to make some generalizations.
A number of assumptions were used in the LCA analysis, including:
- Average field acreage for eastern North Carolina
- Uniform emission values
- No annual or seasonal variation
- Production of lubricants was similar to residual fuel oil
- Tractor trailer assumed to get 6 miles to a gallon, 1000 bushel capacity
- Lime use calculated from nitrogen use and type (1.97 times nitrogen addition)
- Corn seed weight of 1200 seed per pound
- Yield of 160 bushel per acre at 18% moisture content (wet basis)
The LCA report was formatted as a North Carolina Extension Service publication. Enough information was provided about the analysis to be informative without much of the boilerplate included in many professional LCA reports. A specific critical review was not deemed necessary, but the publication was peer reviewed by a number of scientists in the field.
Life Cycle Inventory Analysis
Microsoft Excel was used to calculate inventory values of material inputs for equipment use (Table 4) and commodity inputs (Table 5). Any values not referenced in Table 6 came from production knowledge and general trends for corn grain production in eastern North Carolina.
The US Life Cycle Inventory Database (US LCI, 2013) was used to convert commodity products into subsequent emissions along their life cycles. The database consisted of a number of modules from varying sources appropriate for the United States. Some of these modules integrated all aspects of production (e.g., fuel use, transportation, and inputs) while others did not; information on the inclusion of these factors was provided in each module. The integration of modules to produce nitrogen fertilizer is shown in Table 7, including manufacture and raw material acquisition. After these values were compiled, a decision on energy use and transportation accounting was required.
For this analysis, a single iteration approach was used to calculate emissions related to energy use and transportation.
First, all inputs were taken into account, similar to Table 7, and the total energy use and transportation values were calculated. Next, all energy and transportation emission values from the category summation were included as direct emissions, disregarding the associated energy use and transportation values of these embedded emissions, and thus halting a continual loop at a single iteration. This process created a database of life cycle emissions related to each product and operation. It was possible to use a multiple iteration procedure, since transportation and energy use are embedded in their own production, but a single iteration approach was deemed adequate for this analysis. Creating a life cycle inventory database compiled in a spreadsheet was a long and tedious process, but LCA software packages do this automatically (US LCI modules are able to be used within most major software packages).
Use of other LCI resources may be advisable when a single database either does not contain, or has limited information on, a specific input. For this analysis, energy use data from Shapouri et al. (2002) was used for herbicide and phosphorous production. These energy values were given emissions related to energy values computed in the single iteration LCI process outlined above. This method disregards extraction and processing emissions related to these commodities but was a better option than excluding these processes entirely.
Using the emission database produced with the single iteration method from the US Life Cycle Inventory Database (US LCI, 2013) and the use values given in Table 5, the life cycle emissions were determined on an acreage and bushel basis, with an abridged list of emissions shown in Table 8.
Nitrogen emission values were calculated from Lammel (2000), converted from ammonia nitrogen, and phosphorous leaching values were used from Siegerist and Pfister (2013) (Table 9).
Life Cycle Impact Assessment
The Tool for the Reduction and Assessment of Chemical and Other Environmental Impacts (TRACI, 2013) was used to determine mid-point impacts. Table 10 shows an example of the calculation process related to global warming potential.
A series of environmental impacts were calculated for the total system (Table 11). For this analysis, no normalization or weighting factors were used to aggregate impacts.
Interpretation
Values published by Kim et al. (2009) were converted for direct comparison with the impacts determined in this example (Table 12). Using ammonia as a reference impact, categories were modified to the impact categories used in this analysis between the TRACI Database (TRACI, 2013), acidification (Jolliet et al. 2003), and eutrophication (GHK, 2006).
The acidification and eutrophication values from this example (Table 11) were slightly higher than the overall values calculated from Kim et al. (2009) (Table 12) but were relatively similar. The global warming values were considerably lower in this study, but the values in Kim et al. (2009) take into account tillage operations (field emissions of Table 12). When this difference was taken into account, the global warming values were relatively similar. When trying to compare two different LCA studies using different system boundaries, functional units, input values, and other characteristics, it is common to observe variations.
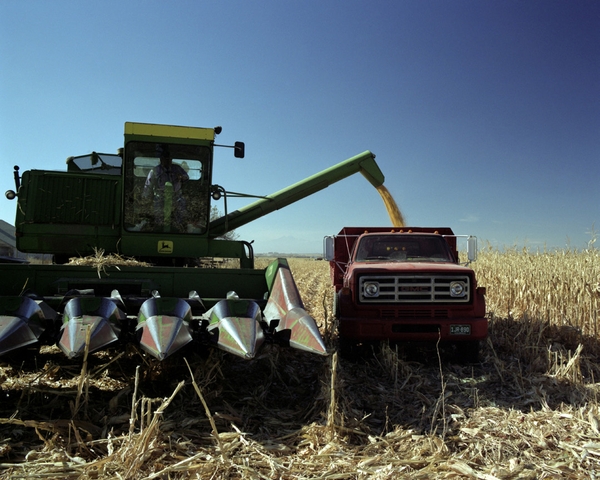
Current ethanol production is primarily from the starch in kernels of field corn. NREL researchers in the DOE Biofuels Program are developing technology to also produce ethanol from the fibrous material (cellulose and hemicellulose) in the corn stalks and husks or other agricultural or forestry residues.
Photo by Warren Gretz, NREL 10460.
Conclusion
This publication should be used as a tool to help the public understand the process behind life cycle assessment methodology. The included example is meant for educational purposes to highlight the possibilities of using LCA to account for more than carbon and the opportunities to add complexity by altering system boundaries. Modification to the goals and scope of the system described here can potentially cause significant differences in results. Nevertheless, life cycle assessment provides a systematic process for determination of environmental impacts throughout a product life cycle and continues to provide worthwhile insight for improving environmental stewardship.
Acknowledgments
The authors would like to acknowledge former North Carolina Extension Specialist Dr. Matthew W. Veal, Ph.D. for his innovation and leadership in development of this publication.
References and Resources
The following resources were used in the publication of this article. These resources provide more information on these topics and would be useful for developing a carbon accounting or LCA methodology.
ACC. 2011. Cradle-to-Gate life cycle inventory of nine plastic resins and four polyurethane precursors. Plastics Division of the American Chemistry Council (ACC). Prepared by: Franklin Associates: Prairie Village, KS.
ASPEN. 2013. aspenONE V8. AspenTech. Retrieved August 10, 2013.
Bare, J., P. Hofstetter, D. Pennington, and H. Haes. 2000. Life Cycle Impact Assessment Workshop Summary- Midpoints versus Endpoints: The Sacrifices and Benefits. International Journal of LCA 5(6): 319-326.
Ecoinvent. 2013. Ecoinvent database v3.0. Retrieved August 10, 2013.
Edwards, W. 2009. Estimating Farm Machinery Costs (PM- 710). Ag Decision Maker File A3-29. Iowa State University Extension: Ames, IA.
EIOLCA. 2013. Economic Input-Output Life Cycle Assessment. Carnegie Mellon University: Pittsburgh, PA. Retrieved August 10, 2013.
GaBi. 2013. GaBi v6. PE International. Retrieved August 10, 2013.
GREET. 2013. The Greenhouse Gases, Regulated Emissions, and Energy Use in Transportation Model.US Department of Energy Argonne National Laboratory: Lemont, IL. Retrieved August 10, 2013.
GHK. 2006. A study to examine the benefits of the End of Life Vehicles Directive and the costs and benefits of a revision of the 2015 targets for recycling, re-use and recovery under the ELV Directive. Final Report to DG Environment. May 2006.
Hanna, M. 2001. Machinery Management- Estimating Field Capacity of Farm Machines (PM-696). Iowa State University- University Extension: Ames, IA.
Hanna, M. 2005. Fuel Required for Field Operations (PM-709). Ag Decision Maker File A3-27. Iowa State University- University Extension: Ames, IA.
Heller, M.C., G.A. Keoleian, and T.A. Volk. 2003. Life cycle assessment of a willow bioenergy cropping system. Biomass and Bioenergy 25(2): 147-165.
ISO. 2006a. Environmental management- Life cycle assessment-principles and framework (ISO 14040: 2006 (E)). International Organization for Standardization: Geneva, Switzerland.
ISO. 2006b. Environmental management- Life cycle assessment-requirements and guidelines (ISO 14044: 2006 (E)). International Organization for Standardization: Geneva, Switzerland.
Jolliet, O., M. Margni, R. Charles, S. Humbert, J. Payet, G. Rebitzer, and R. Rosenbaum. 2003. IMPACT 2002+: A New Life Cycle Impact Assessment Methodology. Int. J. LCA 8(6): 324-330.
Kim, S., B.E. Dale, and R. Jenkins. 2009. Life cycle assessment of corn grain and corn stover in the United States. Int J Life Cycle Assess 14: 160-174.
KSU. 2013. Extension Agronomy e-Updates (Number 391; March 1, 2013). Kansas State University, section 1. Corn seeding rate recommendations. Author: Jim Shroyer. Accessed: November 23, 2013.
Lammel, J. 2000. Environmental Aspects of Fertilizer Production and Use- Consequences for Fertilizer Types and Use. Hydro Agri Deutschland GmbH, Germany.
Lucier, A. 2010. A Fatal Flaw in Manomet’s Biomass Study. The Forestry Source, September 2010: 4.
Manomet Center for Conservation Sciences. 2010. Massachusetts Biomass Sustainability and Carbon Policy Study: Report to the Commonwealth of Massachusetts Department of Energy Resources. Walker, T. (Ed.). Contributors: Cardellichio, P., Colnes, A., Gunn, J., Kittler, B., Perschel, R., Recchia, C., Saah, D., and Walker, T. Natural Capital Initiative Report NCI-2010-03. Brunswick, Maine.
NCSU. 2013. The North Carolina Corn Production Guide: Basic Corn Production Information for North Carolina Growers. North Carolina State University- NC Cooperative Extension: Raleigh, NC.
Shapouri H., J.A. Duffield, and M. Wang. 2002. The Energy Balance of Corn Ethanol: An Update. US Department of Agriculture, Office of the Chief Economist, Office of Energy Policy and New Uses. Agricultural Economic Report No. 813, Washington DC.
Siegerist S., and S. Pfister. 2013. Calculating Crop-Dependent Spatially Differentiated Phosphorus Emissions from Agriculture. In: Proceedings from the LCA XIII International Conference. October 1-3, 2013. Orlando, FL, United States.
SimaPro. 2013. SimaPro 7.3 LCA tool. PRe-sustainability. Retrieved August 10, 2013.
TRACI. 2013. Tool for the Reduction and Assessment of Chemical and Other Environmental Impacts. US Environmental Protection Agency, National Risk Management Research Laboratory: Cincinnati, OH. Retrieved August 10, 2013.
US LCI. 2013. US Life Cycle Inventory Database. US Department of Energy National Renewable Energy Laboratory: Golden, CO. Retrieved August 10, 2013. http://www.nrel.gov/lci/.
USB. 2012. Farm to Market: A Soybean’s Journey from Field to Consumer. Prepared for: United Soybean Board, US Soybean Export Council, Soy Transportation Coalition. Prepared by: Informa Economics. July 2012.
USDA. 1999. Crop Profile for Corn in North Carolina. US Department of Agriculture, Southern IPM Center. Authors: John van Duyn and Ronnie Heiniger. IPM Center at North Carolina State University. Retrieved: November 23, 2013.
USDA. 2005. Forest Residue Trucking Model v.5 (FoRTSv5). US Department of Agriculture, US Forest Service: Auburn, AL.
USDA. 2011. Agricultural Prices (ISSN 1937-4216). US Department of Agriculture, National Agricultural Statistics Service, Agricultural Statistics Board: Washington, DC.
Usbeck, V.C., J. Pflieger, and T. Sun. 2011. Life cycle assessment of float glass. Glass for Europe—Europe’s Manufacturers of Buildings, Automotive and Transport Glass. Prepared by: PE International. Leinfelden-Echterdingen, Germany.
Publication date: Feb. 10, 2015
AG-795
Recommendations for the use of agricultural chemicals are included in this publication as a convenience to the reader. The use of brand names and any mention or listing of commercial products or services in this publication does not imply endorsement by NC State University or N.C. A&T State University nor discrimination against similar products or services not mentioned. Individuals who use agricultural chemicals are responsible for ensuring that the intended use complies with current regulations and conforms to the product label. Be sure to obtain current information about usage regulations and examine a current product label before applying any chemical. For assistance, contact your local N.C. Cooperative Extension county center.
N.C. Cooperative Extension prohibits discrimination and harassment regardless of age, color, disability, family and marital status, gender identity, national origin, political beliefs, race, religion, sex (including pregnancy), sexual orientation and veteran status.