Contents
Introduction
Boom Sprayers
Check Nozzles for Uniform Output
Selecting the Proper Nozzle Tip
Spreaders
Checking the Distribution Pattern and Swath Width
Measuring the Application Rate
Weigh Before and After Methods
Measuring the Area to be Treated
References
Acknowledgments
Introduction
Proper application of pesticides and fertilizers is possible only with a sprayer or spreader that is accurately calibrated. When equipment is not correctly calibrated, it is easy to apply too little or too much pesticide and fertilizer. That may result in a lack of pest control, damaged turf, excess cost, and contamination of the environment.
Calibration is the process of measuring and adjusting the output of application equipment in order to apply the correct amount of material uniformly over a given area. Although this publication focuses on boom sprayers and granular spreaders used on turfgrass, the calibration principles are the same regardless of the type of equipment used. Sprayers and spreaders should be calibrated at first use and after every fourth application. The time it takes to calibrate application equipment is returned manyfold.
Boom Sprayers
Calibrating Output
The output of boom sprayers is affected by sprayer speed, nozzle flow rate, and nozzle spacing.
Sprayer Speed
It is critical to maintain a consistent travel speed during calibration and application. A change in speed will have a direct effect on the amount of chemical applied. As speed increases, the amount applied decreases.
The reverse is also true. For example, if a sprayer traveling at 3 miles per hour (MPH) applies 20 gallons per acre (GPA), increasing the speed to 6 MPH would decrease the amount applied to 10 GPA if the pressure remained constant (Figure 1).
Measuring Ground Speed
Don’t rely on speedometers to determine actual travel speed. Use the following steps to calculate speed in MPH.
- Mark a 200-foot course on terrain that is typical of the surface and soil conditions of the area to be sprayed.
- Fill the spray tank one-half full with clean water.
- Extend the booms of the sprayer.
- Test to determine which gear and RPM will allow the sprayer to maintain the desired pressure on the nozzles while maintaining a constant speed between 3 and 5 MPH. Drive the sprayer through the 200-foot course three times (Figure 2), recording the time of each run (in seconds). Start far enough away from the course to reach the desired speed before passing the first marker.
Average the three test run times:
Average time of sprayer to cross 200 feet =Time 1 + Time 2 + Time33
- Calculate the miles per hour.
MPH= Distance (feet) × 60Average Time (seconds) × 88
Example: You have set up your 200-foot distance, made three test runs, and logged the following times:
-
Time 1 = 31.5 seconds
-
Time 2 = 30.3 seconds
-
Time 3 = 29.2 seconds
Now determine the average time as follows:
Average Time =31.5 + 30.3 + 29.23=30.3
Fill in the average time to determine the MPH.
MPH= 200 feet × 6030.3 seconds × 88=4.5
-
Nozzle Flow Rate
Nozzle flow rate is the amount of liquid sprayed from the nozzle in a given amount of time. The flow rate through a nozzle varies with the size of the tip, sprayer pressure, and the density of the liquid being sprayed.
The nozzle tip is perhaps the most important, yet most neglected, component of the sprayer. It is critical to use the appropriate nozzle tip for the intended pest target and turf conditions (see section on Selecting the Proper Nozzle Tip). The nozzle tip determines the spray pattern and droplet size. The main spray patterns are cone and flat fan shapes. Some special purpose nozzle tips or devices produce raindrop, flooding, and wide-angle fan or cone-shaped patterns. For examples of nozzle types, see Figure 3. Flat fans are most often used to apply herbicides, whereas cones are more appropriate for fungicides and insecticides. Commonly used nozzles have spray angles of 80° or 110°. Wide-angle types (110°) can be mounted lower to the ground or spaced further apart on the boom. Figure 4 illustrates several nozzle-related terms.
The output and droplet size will vary with the size of the nozzle tip orifice or opening. Manufacturers typically code their nozzles with a numbering system to indicate spray angle and output for a particular nozzle. Flat fan nozzles are typically coded with four or more numbers. The first set of numbers indicates the spray angle, and the second set of numbers indicates the nozzle output in gallons per minute (GPM) at 40 pounds of pressure per square inch (psi). For example, an 8003 tip has an 80° angle and applies 0.3 GPM at 40 psi.
Maintaining consistent pressure is also critical for proper application, but changes in pressure do not have the same directly proportional influence on application rate as speed does. For example, in order to double the spray output, the pressure must be increased by four times (Figure 5).
Because of this relationship, pressure cannot be used to make major changes in application rate, but it can be used to correct minor changes due to nozzle wear. To obtain a uniform spray pattern and minimize drift hazard, you must keep the operating pressure within the manufacturer’s recommended range for each nozzle type. Generally a pressure range of 10 to 30 psi is appropriate for herbicides, and a range of 30 to 50 psi is appropriate for insecticides and fungicides. Make sure you keep the pressure within manufacturer’s specifications. Excessive pressure produces inconsistent output and smaller droplets that are more likely to drift. Low pressure results in a weak spray pattern and poor coverage. Due to the configuration of hoses and the presence of couplings and check valves, spray pressure at the nozzle tip is usually lower than the boom pressure indicated on the pressure gauge. Insert a pressure gauge in place of the nozzle tip at various intervals along the boom to compare pressure readings with the main pressure gauge. The pressure at the nozzle is the actual operating pressure.
The density of a liquid is determined by its weight (pounds) per gallon. Density affects the rate at which a liquid will flow and thereby affects its output from a sprayer. Typically, the procedures used to calibrate a sprayer or select a nozzle tip are based on using clean water. Spraying solutions other than water, such as liquid fertilizer, may affect the nozzle flow rate because fertilizer is more dense than water. Nozzle manufacturers’ catalogs contain conversion tables to help you choose the correct size nozzle or to convert sprayer output. The conversion factors are based on the specific gravity of the liquid, a factor that relates the density of the liquid to water, which weighs 8.34 pounds per gallon. You may find it more convenient to conduct the calibration using the liquid fertilizer instead of water, but make certain to wear the proper protective equipment when using active ingredients. (If the fertilizer will be diluted in water, use water for the calibration test.)
Nozzle Spacing
Nozzle spacing is the distance, in inches, between two nozzles on the boom. Nozzle spacing directly affects the spray application rate. Doubling the nozzle spacing decreases by one-half the gallons per acre (GPA) applied (Figure 6).
The type of nozzle used for the application determines nozzle spacing. To uniformly spray with proper overlap across the entire boom, the nozzles must be properly spaced along the boom and mounted at the proper height above the target (Figure 7a and Figure 7b). Spray overlap is the area that gets covered by more than one nozzle.
Most nozzles are spaced 10, 20, 30, or 40 inches apart along the boom. Standard flat fan nozzles should also be aligned at a slight angle to the boom (Figure 8). Newer nozzle caps are designed to obtain this angle when the tip is secured in place on the nozzle body. This prevents the outer edge of adjacent spray patterns from colliding to produce a heavy concentration of spray midway between adjacent nozzles. Cone nozzles should be angled at 35° to 45° from vertical for uniform spray distribution. Refer to the nozzle supplier’s catalog to determine the appropriate nozzle spacing, position, and height that will result in the spray pattern uniformity that you need.
Pre-calibration Checkup
Before you begin to calibrate the equipment, check it carefully to be sure that all components are clean and working correctly. Then follow these guidelines to prepare your sprayer for calibration.
- Be sure your nozzle tips are the correct type and size for the spray application you want to make. See sections on Nozzle Flow Rate and Selecting the Proper Nozzle Tip if you need to change nozzle tips. Make sure that all nozzles are the same type and size along the boom.
- Remove nozzles and screens and clean them in soapy water with a soft brush. Remove any deposits from the nozzle opening with a toothpick (discard after use) or compressed air. (Never use a knife or metallic object to clean nozzles. It will ruin them.) Never try to unclog a nozzle by blowing through it with your mouth.
- In a place away from any wells or water supplies, rinse the spray tank thoroughly and partially fill it with clean water.
- Pressurize the sprayer and flush hoses and boom with plenty of water.
- Reinstall nozzles and screens, pressurize the sprayer within the recommended range, and check nozzles for uniform spray pattern by spraying water on a paved or bare surface and watching for streaks as the spray dries. Wet streaks that occur directly under the nozzles may result from damaged or worn nozzle tips, low operating pressure, or low boom height. Streaking that occurs midway between adjacent nozzles may result from improper nozzle alignment or boom height. Clogged nozzles may produce streaks anywhere in the spray pattern of the affected nozzle (Figure 9).
Pre-calibration Checkup
Before you begin to calibrate the equipment, check it carefully to be sure that all components are clean and working correctly. Then follow these guidelines to prepare your sprayer for calibration.
- Be sure your nozzle tips are the correct type and size for the spray application you want to make. See sections on Nozzle Flow Rate and Selecting the Proper Nozzle Tip if you need to change nozzle tips. Make sure that all nozzles are the same type and size along the boom.
- Remove nozzles and screens and clean them in soapy water with a soft brush. Remove any deposits from the nozzle opening with a toothpick (discard after use) or compressed air. (Never use a knife or metallic object to clean nozzles. It will ruin them.) Never try to unclog a nozzle by blowing through it with your mouth.
- In a place away from any wells or water supplies, rinse the spray tank thoroughly and partially fill it with clean water.
- Pressurize the sprayer and flush hoses and boom with plenty of water.
- Reinstall nozzles and screens, pressurize the sprayer within the recommended range, and check nozzles for uniform spray pattern by spraying water on a paved or bare surface and watching for streaks as the spray dries. Wet streaks that occur directly under the nozzles may result from damaged or worn nozzle tips, low operating pressure, or low boom height. Streaking that occurs midway between adjacent nozzles may result from improper nozzle alignment or boom height. Clogged nozzles may produce streaks anywhere in the spray pattern of the affected nozzle.
Check Nozzles for Uniform Output
The biggest challenge in using a boom sprayer is to obtain a similar output from all nozzles. Measure the output from each to be sure that they all are releasing similar amounts of spray.
- Find a container marked in ounces. With the sprayer operating at the desired pressure, catch the output from each nozzle for 20 seconds and write down the number of ounces from each nozzle.
- After catching the spray from each nozzle individually, add the amounts caught and divide by the number of nozzles to get the average output per nozzle.
- If the output from any nozzle is more than 10 percent above or below the average, clean or replace that nozzle.
- Recheck the output from all nozzles. Use the new output to figure a new average. Make appropriate nozzle changes, if necessary.
Example of Nozzle Output Check:
Test #1 (Ounces after 20 sec.) |
Test #2 (Ounces after 20 sec.) |
|
---|---|---|
Nozzle 1 | 16 | 15 |
Nozzle 2 | 12 | 16 |
Nozzle 3 | 15 | 15 |
Nozzle 4 | 16 | 16 |
Nozzle 5 | 16 | 16 |
Nozzle 6 | 15 | 15 |
Nozzle 7 | 14 | 15 |
Nozzle 8 | 19 | 17 |
Total: | 123 ounces | 125 ounces |
divided by 8 nozzles | divided by 8 nozzles | |
Average | = 15.4 ounces | = 15.6 ounces |
Output Test #1, average: 15.4 ounces
10% of 15.4 is 1.54 (0.10 x 15.4 = 1.54). Round to 1.5. Acceptable range is 13.9 to 16.9 ounces (15.4 ± 1.5). In this case nozzle 2 and nozzle 8 should be checked, cleaned, or replaced. When output is too high, the nozzle is probably worn out and should be replaced. When output is too low, the nozzle may be clogged, and cleaning may bring it into the correct range.
Output Test #2, average: 15.6 ounces
10% of 15.6 is 1.56 (0.10 x 15.6 = 1.56). Round to 1.6. Acceptable range is 14 to 17.2 ounces (15.6 ± 1.6). All nozzles now fall within the acceptable range.
Selecting the Proper Nozzle Tip
The nozzle type and size must be carefully chosen for each particular treatment (Figure 10).
Selection of the appropriate nozzle type is based primarily upon the target pest. In general, flat fans are more appropriate for weed control, and cone types are better for insects and diseases. However, there are exceptions when considering the activity of the pesticide. For example, flat fans are better for spraying contact insecticides, whereas cones are better for applying systemic insecticides. Nozzle suppliers’ catalogs have information to assist you with this decision.
The size of the nozzle tip will depend upon the application rate in gallons per acre (GPA), ground speed in miles per hour (MPH), and effective sprayed width (W) or number of inches between nozzles on the boom. GPA, MPH, and W are used to determine the gallons per minute (GPM) required for each nozzle to provide the desired flow rate. By following these five steps, you can select the nozzles required for each application.
-
Refer to the pesticide or fertilizer label for the recommended spray application rate in gallons per acre (GPA) for your situation. The spray application rate is the gallons of carrier (water, fertilizer, etc.) and pesticide (or fertilizer) applied per acre. When using a carrier other than water, multiply the desired GPA by a conversion factor listed in the nozzle supplier’s catalog and use that value for GPA in Step 4 below.
-
Follow the steps in the section on Measuring Ground Speed (page 3) to determine your actual speed in miles per hour (MPH) under field conditions.
-
Determine the effective sprayed width (W) per nozzle in inches. Measure the distance between two nozzles, center to center, on the boom.
-
Determine the flow required from each nozzle in gallons per minute (GPM) by inserting the values determined in Steps 1 through 3 into the following equation:
GPM (per nozzle)= GPA× MPH×W5,940 -
Refer to a nozzle supplier’s catalog to select the nozzle size that will give the desired output determined in Step 4 at the speed and pressure you intend to use.
Example:
You want to apply a herbicide at 15 GPA, at a speed of 5 mph, using flat fan nozzles spaced 20 inches apart on the boom. What nozzle tip should you select? The required flow rate from each nozzle is as follows:
GPM = 15 × 5 × 205,940=1,5005940=0.25
The nozzle that you select must have a flow rate at 0.25 GPM when operated within a desired pressure range.
When selecting a nozzle tip, it is important to consider the potential for spray drift. A nozzle’s spray pattern is made up of numerous spray droplets of varying sizes. The key to reducing drift is to reduce the number of fine particles, or small-sized droplets, within the spray volume while still maintaining your spray pattern for even coverage. Special features, or subtypes like “extended range,” are available for some nozzle types that produce a greater percentage of large droplet sizes over a wide range of pressures.
Referring to a chart of flat fan nozzle tips in the Spraying Systems Co. catalog, we find that the TP8003 (flat fan spray tips) produces 0.26 GPM at 30 psi and thereby provides the correct output.
However, an XR8004 Extended Range flat spray tip operated at a more desirable pressure range of 15 to 20 psi would achieve the correct output while minimizing the risk of drift.
After choosing the right nozzles, make sure that they are set at the correct spacing, height above the target, and orientation on the boom.
Measuring Output
Measuring Output With New Nozzles
Now that you have selected and installed the proper nozzle tips (Steps 1 through 5), you are ready to complete the calibration of the sprayer by following these additional steps:
- Convert the GPM output for each nozzle (Step 4) to ounces per minute (OPM):
GPM x 128 = OPM (1 gallon = 128 ounces)
In our example: 0.25 GPM x 128 = 32 OPM
- While the sprayer is stationary and the system pressurized, collect the output from the nozzle closest to the average output during the pre-calibration check (“quick-check nozzle”) for 30 seconds and multiply by 2 or collect all of the output for one minute (Figure 11). Designating a quick-check nozzle allows sprayer output to be measured quickly and easily any time the sprayer is used. However, the more nozzles you collect from, the more accurate the calibration. Calculate the average output from the nozzles sampled.
- If the output measured (Step 7) is within 5 percent of the desired OPM (Step 6), the sprayer is calibrated accurately. If you are not within the 5 percent margin, you need to adjust the output (see Making Adjustments below).
Measuring Output With Existing Nozzles
- Pressurize the sprayer to the desired operating pressure while it is parked. Collect the output in a container marked in ounces from a nozzle or several nozzles as described in Step 7 above to determine the nozzle flow rate in ounces per minute (OPM).
-
Convert OPM (Step 1) to GPM. Divide OPM by 128.
-
Determine sprayer speed (MPH) as described above.
-
Measure nozzle spacing (W) as described above.
-
Determine sprayer output in gallons per acre (GPA) by inserting the values determined in Steps 2 through 4 into the following equation:
GPA= GPM × 5940MPH × W
To determine the equivalent gallons per 1,000 square feet, divide the GPA by 43.56.
Example:
The average nozzle output from your boom sprayer is 44 OPM or 0.34 GPM (44/128). The sprayer speed is 4.5 MPH and nozzles are spaced 20 inches apart on the boom. What is the sprayer output in gallons per acre? What is the output in gallons per 1,000 sq. ft.?
GPA= 0.34 × 59404.5 × 20= 22.4
Gallons per 1,000 sq. ft. = 22.4 GPA43.56= 0.51
If the sprayer output is not within 5 percent of the GPA recommended on the product label, adjust the output as explained in the following section.
Making Adjustments
Spreaders
The most common types of spreaders used to apply dry pesticides and fertilizers to turfgrass are drop spreaders and rotary spreaders. For convenience, choose a model that is easy to fill and clean.
Drop spreaders (Figure 13) have a uniform pattern within the swath of application, low drift potential, and precise control of the edges of the patterns. This makes them useful for edging around small areas, such as driveways and flowerbeds, or near environmentally sensitive areas, such as ponds or streams. Because the edge of a drop-spreader pattern is abrupt, even a small error in steering will result in untreated or over-applied strips. Also, the drop spreader may damage the coating on large granules.
Rotary spreaders cover a wider area faster and are preferred for larger areas. Steering errors also are less critical. Compared with drop spreaders, rotary spreaders are easier to push, have better ground clearance, and are not as easily knocked out of calibration. Drift may be a problem with fine particles on windy days. Generally, rotary spreaders are less precise in uniformity and distribution than drop spreaders. Temperature and humidity may also affect the distribution pattern.
The application rate and distribution patterns of rotary spreaders and, to some extent drop spreaders are affected by design, product, environment, and operator.
Spreader Design
Characteristics of the impeller (spinning disc or plate) such as diameter, speed (gear ratio), shape (flat or concave), fin shape and angle, and height above the ground directly effect swath width and distribution pattern. These characteristics are determined by the manufacturer. Some spreaders have an adjustable port or a pattern adjustment that affects the drop point of the product onto the impeller.
Application Product
Characteristics of the fertilizer or pesticide, such as particle shape, size, uniformity, density, critical relative humidity (the humidity at which the fertilizer becomes sticky), and surface friction, all affect distribution and flow rate. Recalibrate your equipment whenever you change from one material to another.
Environment
Wind speed and direction obviously effect distribution, but temperature and relative humidity are also important. You need to decide if applications should be made under current conditions or postponed until conditions become acceptable. The flow rate with the same product may change from day to day as temperature and humidity change.
Spreader Operator
The walking speed, handle height, and pattern of travel are controlled by the operator. Always hold the spreader handle at the proper height to keep the impeller level. Correct application depends on the applicator walking at the same speed during calibration as during actual application. Walk at a pace that you can comfortably and consistently maintain over the whole time you intend to operate the spreader. Three MPH is considered a standard walking speed when pushing a spreader.
Practice one of the following methods to achieve a consistent walking speed: synchronize your pace with a portable metronome, count paces to the same tempo, or record the time it takes to walk a measured distance.
The following table converts the time it takes to walk 100 feet in MPH. It is based on the same formula used for measuring travel speed of boom sprayers.
Speed in MPH |
Time in seconds to travel a distance of 100 feet |
---|---|
1.0 | 68 |
1.5 | 45 |
2.0 | 34 |
2.5 | 27 |
3.0 | 23 |
3.5 | 19 |
4.0 | 17 |
4.5 | 15 |
5.0 | 14 |
Calibrate all granular spreaders under similar conditions and with the specific operator and product to be used in the actual application.
Calibration of granular spreaders is a two-part process that requires:
- Observation of the distribution pattern.
- Determination of the application rate.
Techniques for measuring the distribution pattern and the application rate will depend on the spreader type.
Checking the Distribution Pattern and Swath Width
It is critical to check the distribution pattern of spreaders so that you will not end up applying too much product to some areas and not enough to others even if the application rate is correct.
Because granules drop straight down the opening of drop spreaders, the distribution pattern should be uniform across its swath. The swath of a drop spreader is simply the width of the bottom of the hopper. Approximate the correct orifice opening for your drop spreader based on label recommendations. Make a small test run on a clean, paved surface, and observe the distribution pattern. Any unevenness may be due to clogging of the openings in the bottom of the hopper or agitator malfunctions that will need to be corrected.
Rotary spreaders are a different matter: their distribution pattern must be checked frequently. The distribution pattern will be different with each product because some types of granules will travel farther than others. The preferred method for checking the distribution pattern of rotary spreaders involves laying out a row of shallow boxes, trays, or pans on a line perpendicular to the spreader’s direction of travel.
Place one box in the center with enough space on either side to allow the spreader wheels to pass through. Space the remaining boxes on 2-foot centers to either side of the center box, as shown in Figure 14. All boxes must be identical in size, typically 1 to 2 inches deep, with an area of at least 1 square foot. There should be an odd-number of boxes in the row covering 1½ to 2 times the anticipated effective swath width. Place a piece of cloth in the bottom of each box to keep particles from bouncing out.
Pour some product into the rotary spreader and choose the setting recommended on the label. Make at least three passes over the boxes to obtain an accurate assessment of the distribution pattern. Be sure to operate in the same direction and position on every pass. Weigh the granules collected in each box and plot a distribution pattern, or pour the granules from each box into its own vial or small bottle. The vials must be identical in size and shape. When the vials are placed side by side in the same order as the collection boxes, a plot of the distribution pattern is visible, as shown in Figure 15.
Ideally the contents of the vials form a bell-shaped curve that peaks in the center and descends evenly on each side. Determine which have one-half the amount of product in the center vial. The distance between these boxes is the effective swath width. Use this figure to space spreader passes.
For example, if the center vial has material that is 2 inches deep, and the vials from the 6-foot positions (6 feet left of the spreader centerline and 6 feet right of the spreader centerline) have material 1 inch deep, the effective swath width is 12 feet. If it appears that the half rate falls between two boxes used in the test, take the mid-point between those boxes as half the effective swath width. For example, you estimate that the half-rate volume falls between boxes located 4 and 6 feet to the left and 4 and 6 feet to the right of center. The effective swath width is 10 feet (5 feet left and 5 feet right of the centerline).
If the two boxes used to determine effective swath width do not contain the same amount of product (non-symmetrical pattern), adjust the spreader to correct the pattern. Follow the manufacturer’s recommendation on pattern adjustment. Certain models allow you to block off part of the metering port(s) or move the drop point of the granules on the impeller.
Checking the pattern over a paved area is a quicker, though less accurate, method to estimate the distribution pattern. Particle bounce and scatter make this method inexact, but it does reveal gross distribution errors. A rough estimate of the effective swath width can be made by measuring the central two-thirds of the total swath.
Measuring the Application Rate
When selecting an area in which to check calibration, make certain that it is an acceptable application site, or plan to collect the granules in a device that prevents their contact with the ground. Be aware that repeated applications to the same area, as is common with calibration trials, can damage turf.
Drop Spreader
Several methods for checking the application rate of a drop spreader are described below. Be certain to walk at the desired speed before starting the flow of granules when crossing the starting point. At the finish point, stop the flow, but continue walking.
Catch-Pan Method
Attach a catch pan or small section of gutter with end caps that is wide enough to capture all the granules leaving the bottom of the hopper. Make certain that the catch pan is hung on the spreader so that there is no interference with the shut-off bar or rate-control linkage. (Figure 16).
The catch-pan method is outlined below:
- Measure a straight test course that will give the equivalent of 100 square feet. For example, a drop spreader with a 3-foot swath should cover 33 feet (100/3); a spreader with a 2-foot swath should cover 50 feet (100/2).
- Place some product in the hopper and select a gate setting based on the product label or spreader manual only as the initial starting point.
- Push the spreader over the test course. Be sure to start the flow of material at the beginning of the test course and stop it exactly at the end. Remove the captured material and weigh it in ounces or grams using a digital scale. Convert ounces or grams to pounds (see Table of Measurements).
- Multiply this amount by 10 to determine the application rate in pounds per 1,000 sq. ft., or multiply the amount collected by 435.6 to determine the rate in pounds per acre.
- Compare the rate delivered by the test run (your application rate) with the label rate. Adjust the gate opening and repeat the procedure until your application rate is within 10 percent of the labeled rate. Small changes in the setting can result in large changes in flow rate.
Example:
You want to calibrate a drop spreader with a 3-foot swath to apply 1 pound of nitrogen per 1,000 sq. ft. using a 27-3-4 fertilizer. This calculates to 3.7 pounds of fertilizer per 1,000 square feet because the fertilizer consists of 27% nitrogen.
1 lb. (rate)0.27 (% nitrogen in decimal form) = 3.7 lbs.
Therefore, the spreader should be calibrated to apply one-tenth of 3.7 pounds or 0.37 pounds of fertilizer when pushed over the 33-foot test course. You collect 196 grams, or 0.43 pounds (196 grams divided by 454 grams per pound), of product after traveling the test course. The calibrated rate is, therefore, 4.3 pounds per 1,000 square feet. This is outside the range of 3.33 to 4.07 pounds per 1,000 square feet, based on the desired rate of 3.7 pounds per 1,000 square feet, plus or minus 10 percent. Because the calibrated rate is too high, the gate opening should be reduced and the calibration process repeated (Figure 17).
Sweep and Weigh Method
Apply the product to a smooth, clean surface, such as cement or a plastic tarp, and sweep and weigh the material. Follow the same steps as above, but keep in mind that if the plastic tarp used is narrower than the swath width of the spreader and granules are collected from the surface of the tarp only, the width of the tarp must by multiplied by its length to determine the size of the calibration area.
Weigh Before and After Methods
You can also determine the amount of material applied by taking before and after weights:
- Place a known weight of granules in the hopper, conduct a trial run, and reweigh the granules remaining in the spreader.
- If a large scale is available, determine the amount applied by weighing before and after the application. The difference in weight is the amount of granules applied to the calibration area.
Example:
You put 2 pounds of granules in a drop spreader that has a swath width of 2 feet. After applying the product to a 50-foot test course, you recover 1.75 pounds of granules from the spreader. The calibrated rate is 0.25 pounds per 100 square feet, or 2.5 pounds per 1,000 square feet.
Rotary Spreader
To ensure uniform coverage with a rotary spreader, apply the product at half the labeled rate in two passes over the area. This is especially important if the distribution pattern is not symmetrical. The goal for calibrating a rotary spreader, therefore, is to verify an application rate that is within 10 percent of one-half the labeled rate.
Collection devices can be used to calibrate a rotary spreader. However, commercially available shrouds that are attached to the spreader are compatible only with a limited number of spreader makes and models. Other devices like plastic bags secured to the bottom of the spreader can interfere with product delivery and cause inaccurate results. Determine the effective swath width before attempting to calibrate a rotary spreader with a collection device.
The easiest way to check the application rate of a rotary spreader is to load the spreader with a weighed amount of product. Rely on your experience with the spreader to select a test setting that will deliver one-half the labeled rate. (Note: spreader settings are not linear; therefore, using a setting number that is half the number recommended on the product label will not result in half the application rate.) Apply the material over a measured distance, and then weigh the product remaining in the spreader to determine the rate actually applied per 1,000 square feet. Use a linear distance that can be easily converted to 1,000 square feet based on the spreader’s effective swath width (see the following table).
Effective Swath Width (feet) |
Distance (feet) |
---|---|
6 | 167 |
8 | 125 |
10 | 100 |
12 | 84 |
14 | 72 |
Multiply the amount collected in covering 1,000 square feet by 43.56 to determine the application rate in lbs. per acre.
Compare the rate delivered by the test run (your application rate) with the label rate. Make appropriate changes in the size of the gate opening and repeat the procedure until your application rate is within 10 percent of the recommended rate.
Example:
A turf herbicide is to be applied at 80 pounds per acre. To help ensure a more uniform application, the herbicide will be applied in two passes. In this case, the spreader should be calibrated to apply the material at 40 pounds per acre. The effective swath width is 12 feet.
Two pounds (908 grams) of product are loaded into the spreader, which is then pushed over an 84-foot calibration course. The amount remaining in the spreader weighs 426 grams. The difference between the original weight and post-calibration weight is 482 grams, or 1.06 pounds (482 grams divided by 454 grams per pound). The spreader is calibrated to apply 1.06 pounds per 1,000 square feet. This is equivalent to 46.2 pounds per acre (1.06 pounds per 1,000 square feet times 43.56). This is outside the range of 36 to 44 pounds per acre, based on the desired rate of 40 pounds per acre plus or minus 10 percent. Because the calibrated rate is too high, the gate opening should be reduced and the calibration process repeated.
Another method is to use the weight of material collected from the box in the center of the pattern distribution test in one of the following equations:
For weight in grams:
grams of material collected in boxarea of box (sq. ft) × number of passes×2.2=lbs. product1,000 sq. ft.
For weight in ounces:
ounces material collected in boxarea of box (sq. ft) × number of passes×62.5=lbs. product1,000 sq. ft.
If the calibrated rate is not within 10 percent of the recommended rate, adjust the gate opening and reapply product to the center box in 3 to 5 passes.
Determining How Much to Apply
After calibrating the spreader, determining the amount of product required for the application is straightforward. Use a measuring wheel or tape to accurately measure the area to be treated. Label application rates typically are provided in pounds of product per acre or per 1,000 square feet. Whether you use acres or 1,000 square feet in your calculations, be consistent. Divide square feet by 43,560 to convert to acres; multiply acres by 43,560 to convert to square feet. To determine the amount of product to apply, multiply the treated area by the application rate.
Example:
A granular insecticide is to be applied at a rate of 2 lbs./1,000 sq. ft. How much will you need to apply to 2.5 acres?
- Convert acres to square feet.
2.5 acres × 43,560 sq. ft. acre= 108,900 sq. ft.
-
Multiply the area by the application rate to get total amount of product needed.
108,900 sq. ft. × 2 lbs. product 1,000 sq. ft.= 217.8 lbs
Operating the Spreader
Follow these guidelines to improve the application
performance of granular spreaders.
Drop Spreaders
Turning a drop spreader sharply will result in an irregular application pattern. Therefore, when treating an area in parallel passes, always turn off the spreader before making turns to start the next pass. Treat both ends (header strips) of the area first (Figure 18). Apply a header strip across each end of a rectangular area or completely around circular or irregularly-shaped areas. This allows you to reach the proper speed when starting in the first strip and shut off the spreader when turning in the strip at the far end to prepare for the next pass.
Use a street, sidewalk, or similar surface along the border to guide your first pass.
To prevent skips or overlap, make certain that the wheels slightly overlap the wheel tracks of the previous pass.
Rotary Spreaders
Getting even coverage can be a challenge with a rotary spreader. The two methods described below are helpful in obtaining an even spread. Accurate spacing of swaths is essential for proper overlap with both methods. The effective swath width serves as the basis for the distance between spreader passes. For example, if the effective swath width is 8 feet, after each pass, move the spreader over 8 feet from the center of the tire tracks to begin the next pass. This will give a fairly consistent rate of application over the entire area.
Where possible, use flags or stakes to mark the effective swath width. When the spreader is positioned in the starting location and direction of the first pass, pace off the effective swath width to the point where the next parallel pass will end. This will serve as a visual “marking post” for the return pass. As you come to the end of the first pass and reposition the spreader to line up with the first stake, place a second stake another “effective swath width” distance away to use as a marker for the following pass. Move the stakes in this fashion at the beginning of each pass until the area is completely treated. If markers cannot be used, focus on an object past the point where you will stop spreading to help make a straight pass.
After the rotary spreader is calibrated to apply the product at half the labeled rate, the application can be made in one of two ways: apply the product in two passes at right angles to each other (Figure 19), or, apply the product in parallel passes spaced apart at half the effective swath width (Figure 20).
When operated backwards, a spreader will deliver a different application rate. If it is desirable to operate a spreader in reverse, as may be necessary when sowing seed on wet or amended soil, the spreader must be calibrated in that direction.
Make turns with the spreader closed, because the application pattern would be irregular while turning. Start walking before opening the gate and close it before stopping.
Be careful to cleanup pesticide and/or fertilizer granules that have fallen on paved or cemented surfaces (Figure 21).
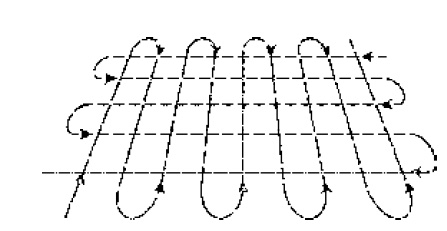
Figure 19. In the “right angle” method, two passes are made perpendicular to each other. This method permits a confirmation that the correct application is being applied if no product remains in the spreader at the completion of the first pass.
Or, if you choose to put enough product in the spreader to treat the entire area with a single load, you should see half the material remaining in the spreader at that point.
Measuring the Area to be Treated
To apply the correct amount of pesticide, you need an accurate measure of the area to be treated. One method for calculating the size of an irregular area is to subdivide it into the closest approximation to geometric shapes, as shown in Figure 22. The area of each shape is calculated separately using the formulas in the box below. For example, the area of Figure 22 can be subdivided into a circle (A), a rectangle (B), a triangle (C), and a trapezoid (D). The total area of Figure 22 is then the sum of the individual areas of A + B + C + D.
A= 3.14 × 70 ft. ×70 ft. = 15,386 sq. ft.
B= 70 ft. × 90 ft. = 15,300 sq. ft.
C= 90 ft. × 50 ft. 2=2,250 sq. ft.
D= 115 ft. × 140 ft.2× 40=5,100 sq. ft.
Total: 38,036 sq. ft.
Area of Geometric Shapes
Circle: area = 3.14 × r2
Rectangle: area = a × b
Triangle: area = b × h2
Trapezoid: area = a + b2× h
Table of Measurements
Length
Standard Measure
- 1 ft. = 12 in.
- 1 yd. = 3 ft.
- 1 mi. = 5,280 ft.
Metric Conversion
- 1 in. = 2.54 cm
- 1 yd. = 0.914 m.
- 1 mi. = 1.61 km.
- 1 m. = 3.281 ft.
- 1 km. = 3,281 ft. = .621 mi.
Area
Standard Measure
- 1 sq. ft. = 144 sq. in.
- 1 sq. yd. = 1,296 sq. in. = 9 sq. ft.
- 1 ac.= 43,560 sq. ft. = 4,840 sq. yd.
Metric Conversion
- 1 sq. ft. = 929 sq. cm.
- 1 sq. yd. = 0.8361 sq. m.
- 1 h. = 2.47 ac.
- 1 ac= 0.405 h.
Volume
Standard Measure
- 1 fl. oz. = 2 tbs. = 6 tsp
- 1 tbs. = 3 tsp.
- 1 cup = 8 fl. oz. = 16 tbs.
- 1 pt. = 2 cups = 16 fl. oz.
- 1 qt. = 2 pt. = 32 fl. oz.
- 1 gal. = 4 qt. = 8 pt. = 128 fl. oz. = 231 cu. in.
Metric Conversion
- 1 fl. oz. = 29.5 ml. = 0.0295 L.
- 1 ml. = 0.033 fl. oz.
- 1 pt. = 437 ml. = 0.437 L.
- 1 qt. = 945 ml. = 0.945 L.
- 1 gal. = 3785 ml. = 3.785 L.
- 1 L. = 33.8 fl. oz. = 2.112 pt. = 1.057 qt. = 0.264 gal.
Weight
Standard Measure
- 1 lb. = 16 oz.
- 1 gal. of water = 8.34 lb.
Metric Conversion
- 1 oz. = 28.35 g.
- 1 lb. = 454 g.
- 1 gal. of water = 3.786 kg.
- 1 ton = 907 kg.
- 1 kg. = 35.27 oz. = 2.205 lb.
Abbreviations
ac. acre
m. meter
cm. centimeter
mi. mile
ft. foot or feet
ml. milliliter
g. gram
oz. ounce
gal. gallon
pt. pint
h. hectare (1h: 10,000 sq. m.)
qt. quart
in. inch
sq. square
kg. kilogram
tbs. tablespoon
km. kilometer
tsp. teaspoon
L. liter
yd. yard
lb. pound
References
- Boerboom, C., C. Ramsay, G. Thomasson, G. Stahnke, and R. Maleike. 1996. Turf and Ornamental Weed Management Principles. Washington State University.
- Guide for Preparing Field Sprayer Calibration Procedures. 2001. Technical Standards of the American Society of Agricultural Engineers. ASAE EP367.2 Jan01.
- Martin, A., T. Gibb, Z. Reicher, and C. Throssell. 2000. “Turf Pest Control, Category 3b.” Pesticide Applicator Training Manual. Purdue University.
- Merrigan, S. D. and P.B. Baker. 1992. Pesticide Applicator Training Manual: Category 3 Turf and Ornamentals, Tucson: University of Arizona.
- Nixon, P., T. Voigt, S. Penix, and R. Wolf. 1996. Illinois Pesticide Applicator Training Manual Turfgrass, Special Publication 39-1. Urbana: University of Illinois.
- Ozkan, H. E. 1991. Calibrating Turfgrass Chemical Application Equipment. Extension Bulletin 817. The Ohio State University.
- Procedure for Calibrating Granular Applicators. 2001. Technical Standards of the American Society of Agricultural Engineers. ASAE EP371.1 Jan01.
- Roberson, G. 1999. Calibrating Field Sprayers, AG-587. North Carolina Cooperative Extension Service.
- Sicheneder, K. 1998. “Turfgrass Pest Management.” A Training Manual for Commercial Pesticide Applicators. Michigan State University Extension Bulletin E-2327.
Acknowledgments
Prepared by Wayne G. Buhler, Pesticide Education Specialist, North Carolina Cooperative Extension Service The author thanks the following for their contributions and assistance:
- Emily Erickson, Crop Science Lecturer
- Matt Martin, Area Specialized Agent, Turfgrass
- Art Bruneau, Extension Turfgrass Specialist
- Gary Roberson, Biological and Agricultural Engineering Specialist
- Joe Neal, Extension Horticulture Specialist, Weed Management
- Fred Yelverton, Extension Crop Science Specialist
This publication was adapted from Water Quality and Sprayer and Spreader Calibration, WQWM-152.
6,000 copies of this public document were printed at a cost of $2,519.00, or $.42 per copy.
Publication date: Nov. 1, 2001
Reviewed/Revised: July 29, 2024
AG-628
N.C. Cooperative Extension prohibits discrimination and harassment regardless of age, color, disability, family and marital status, gender identity, national origin, political beliefs, race, religion, sex (including pregnancy), sexual orientation and veteran status.