Irrigation is practical for many North Carolina farmers. Because irrigation can be expensive, however, there is much to consider before deciding to irrigate. Irrigation equipment may cost more than half as much as the land on which it is used.
Irrigation also consumes large quantities of water and energy. Annual energy costs of $25 per acre are typical in North Carolina, where application rates average about 8 inches of water per acre per year. When irrigation systems are poorly maintained and operated, energy costs may be two to three times that amount. One way to reduce irrigation costs is to optimize the use of water and energy, as described in this publication.
How efficiently irrigation systems use water and energy is determined primarily by the type of system and the way it is operated, maintained, and managed. This publication discusses irrigation decisions that affect water and energy efficiencies.
Comparing the water and energy efficiencies of different systems can be difficult because not all manufacturers use the same terminology. Some of the more common terms are listed at the end of this publication. These definitions are helpful in comparing systems and converting efficiencies to consistent units.
Potential water-use efficiency for the types of irrigation systems most frequently used in North Carolina is shown in Table 1. The word potential means the maximum water-use efficiency that can be achieved when the system is maintained and operated properly. Many factors influence water-use efficiency. Irrigation must be scheduled at the proper times to obtain the efficiencies shown. Irrigation scheduling is the process of determining when to irrigate and how much water to apply. Scheduling strategies are discussed in Extension Service publication AG542-4, Irrigation Scheduling to Improve Water-and Energy-Use Efficiency. Other factors affecting water-use efficiency are discussed further in this publication.
Table 1. Potential Water-Use Efficiencies of Several Types of Irrigation Systems
Type of System | Potential Water Use Efficiency (percent) | Typical Pump Pressure (PSI) |
---|---|---|
Hand-move (sm. sprinkler) | 75 | 60-100 |
Hand-move (gun sprinkler) | 70 | 80-130 |
Solid-set | 80 | 60-100 |
Center pivot (med. pressure) | 90 | 70-110 |
Center pivot (low pressure) | 92 | 40-80 |
Linear-move | 92 | 40-80 |
Hose-pull traveler | 70 | 30-200 |
Drip or trickle | 90+ | 5-75 |
Performance data for most agricultural power equipment marketed in the United States are published annually in the Nebraska Tractor Test Report. The data are obtained by University of Nebraska engineers and can be used to evaluate the energy-use efficiency of irrigation systems. Performance standards are established for engines and pumping plants properly adjusted according to manufacturer recommendations. Nebraska performance standards for irrigation pumping plants are shown in Table 2.
Energy Source | Energy Unit | Horsepower Hours1 Per Unit of Energy | Water Hp-hr2 Per Unit of Energy3 |
---|---|---|---|
Diesel | Gallon | 16.7 | 12.5 |
Gasoline4 | Gallon | 11.5 | 8.66 |
Propane4 | Gallon | 9.2 | 6.89 |
Natural Gas6 | 1,000 cu ft | 88.95 | 66.7 |
Electricity | kWh | 1.187 | 0.8858 |
Source: Dom, T. W., P. E. Fishbach, D. F. Elsenhauer. J. R. Gilley, and L. E. Stateson, It Pays to Test Your Irigation Pumping Plant. Publication EC-713. Lincoln: University of Nebraska. Cooperative Extension Service.
1Horsepower-hours is a measure of the work being accomplished by the power unit with losses considered. ↲
2Water horsepower-hours is the work being accomplished by the pumping plant at the Nebraska Performance Criteria. ↲
3Based on 75 percent pump efficiency. ↲
4Taken from Test D of Nebraska Tractor Test Reports. Drive losses are accounted for in the data
Assumes no cooling fan. ↲
5Manufacturers' data corrected for 5 percent gear-head drive loss and no cooling fan. ↲
6Assumes natural gas energy content of 1,000 Btu per cubic foot. ↲
7Assumes 88 percent electric motor efficiency. ↲
8Direct connection assumes no drive loss. ↲
Water- and energy-use efficiency for irrigation is not identical. But energy is consumed for every gallon of water pumped. For a given system, an increase in water use results in a proportional increase in energy consumption. Any water not actually used by the crop reduces the water-use efficiency and consequently the energy-use efficiency. The first step to reducing energy use is to apply just enough water to satisfy crop needs. This can be accomplished by selecting the system that minimizes water use and then properly maintaining and managing that system.
Selecting the Right Irrigation System
Type of System
There are many types of irrigation systems. They include solid set, permanent, manual-move, lateral-move, side-roll wheel-move, center-pivot, hard-hose traveler, cable-tow traveler, drip or trickle, and subirrigation types. Most farmers have limited choices for their farm or field. Some systems use water and energy more efficiently, whereas others are designed to overcome limitations such as irregular field shapes, sloping land, or a limited water supply. All of these factors must be considered before selecting a system. Consideration should also be given to capital cost; crops to be grown; cultural practices; soils; acreage to be irrigated; availability of labor; the need for environmental modification, chemigation, or fertigation; and dealer availability and service. After these factors have been evaluated, one or two systems will usually emerge that most effectively satisfy the irrigation needs of the site. The following publications discuss features of each type of irrigation system:
- EBAE 150-91, Selection and Management of Efficient Self-Propelled Gun Traveler Irrigation Systems.
- EBAE 151-91, Selection and Management of Efficient Center Pivot and Linear-Move Irrigation Systems.
- EBAE 152-91, Selection and Management of Efficient Low Volume Irrigation Systems.
- EBAE 153-91, Selection and Management of Efficient Hand-Move Solid Set and Permanent Irrigation Systems.
Selecting an Efficient Pumping Plant
The pumping plant is defined as the pump and motor (for electrically driven systems) or engine (for internal combustion systems) plus all associated fittings. Regardless of the type of system selected, most of the energy consumed in irrigation is used by the pumping plant.
Irrigation Pumps. Pumps are usually either of the centrifugal or turbine type. Centrifugal pumps (which may be self-priming or non-self-priming) are used to pump water from surface sources and shallow wells. Turbine pumps (either vertical shaft or submersible) are used to pump from deep wells. Features of each type of pump are discussed in Extension publication AG-389, Water Supplies for Subirrigation, and AG-452-6, Pumping Plant Performance Evaluation.
Some pumps are more efficient than others, as shown in Figure 1 . However, most types of pumps are available over a wide range of operating efficiencies. Pump efficiency is the ratio (expressed as a percentage) of the water horsepower of the discharge water divided by the power delivered to the pump by the motor or engine.
Normally, pump cost increases as efficiency increases (Figure 2), but savings in operating costs usually compensate for this difference after a few years of use. If the pump is likely to be used over a broad range of operating conditions, ensure that it will meet all the required conditions. If possible, the pump should be operated in the midrange of its performance curve.
The efficiencies of individual pump types vary among models, manufacturers, and types. A pump efficiency in the range from 75 to 85 percent is preferable. Once the operating pressure (head) and system capacity (in gallons pff minute) have been determined, pump characteristic curves (Figure 3) should be consulted to select the most efficient pump for the specific conditions.
Power Units. Power-unit efficiency is also important to pumping plant performance. Power sources are of two types: (1) internal combustion engines (either directrive engines used solely for irrigation or tractors equipped with a power takeoff to drive pumps) and (2) electric motors.
Power-unit efficiency is the efficiency with which chemical energy stored in the fuel (for internal combustion engines) or electrical energy (for electric motors) is converted to mechanical energy to drive the pump. Where electricity is available, it is the most efficient power source (Figure 4). As shown in Table 3, the efficiency of electric motors ranges from about 80 percent for motors under 7.5 horsepower to over 90 percent for motors of 75 horsepower or larger.
Electric Motor Size (horsepower) | Full Load Motor Efficiency (percent) |
Matched Size Pump Efficiency1 (percent) |
Typical Attainable Pumping Plant Efficiency2 (percent) |
---|---|---|---|
3-5 | 80-86 | 55-65 | 44-56 |
7 1/2-10 | 85-89 | 60-70 | 51-62 |
15-30 | 86-90 | 65-75 | 56-68 |
40-60 | 88-92 | 70-80 | 62-74 |
75 and larger | 90-93 | 75-85 | 68-79 |
1 Values shown are typical for centrifugal pumps. Submersible pumps typically range 3 to 5 percent higher and turbine pumps range 5 to 10 percent higher for sizes under 75 horsepower. Above 75 horsepower, a few centrifugal pumps may approach efficiencies of 88 percent, while large submersible and turbine pump efficiencies peak at about 90 percent. Since pump efficiencies are quite variable depending on type, manufacturer, and size, consult pump performance curves for a specific application. ↲
2 Values obtained by multiplying power source efficiency range (in this case, for an electric motor) times matched pump efificiency range. ↲
Internal combustion engines are inefficient. Gasoline engines are only 20 to 26 percent efficient, whereas diesel engine efficiencies range from 25 to 37 percent. Performance standards for the different types of power units are listed in Table 2. Over the life of the pumping plant, the difference in operating costs among various types of power units and pumps must be weighed against any savings in initial investment.
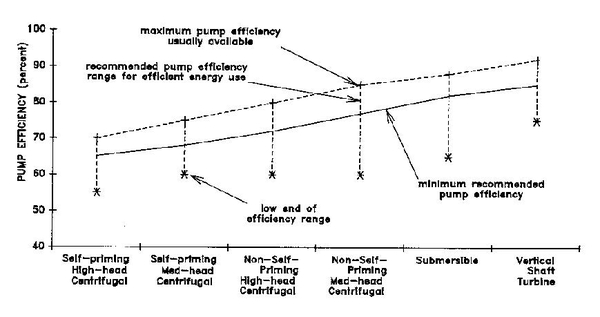
Figure 1. Typical efficiency ranges of irrigation pumps. Most irrigation dealers offer a range of pumps that span the entire efficiency range shown. Values shown are representative for most pumps, but there are exceptions in all categories.
Consult pump characteristic curves to select a pump that provides the desired efficiency for a given set of operating conditions.
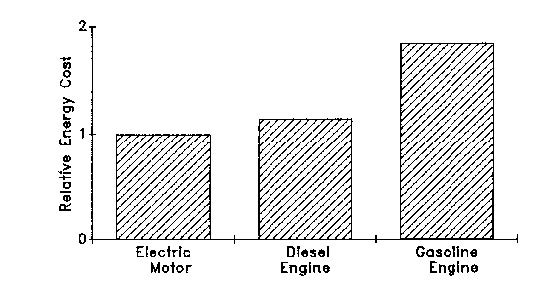
Figure 4. Relative energy cost for power sources most commonly used in North Carolina . All values are based on the recommended Nebraska Performance Standard for the power units shown. Energy costs are based on the following rates: electricity, 7 cents per kilowatt hour; diesel fuel, $1 per gallon; gasoline, $1.10 per gallon. For gasoline engines, the fuel c
Maintaining Irrigation System Efficiency
Well-designed irrigation systems with properly sized pumping plants will normally meet or exceed performance standards during initial use. Over the life of the system, however, mechanical components of the system wear, reducing the overall efficiency of the system. Some common causes of low overall efficiency are summarized in the following sections.
Internal Combustion Engines. Each percentage decrease in engine efficiency increases the amount of fuel used by 3 to 5 percent. For example, fuel consumption increases by 19 percent for the gasoline engine shown in Figure 5 as the engine efficiency decreases from 23.8 percent (Nebraska Performance Standard) to 20 percent. For a 100 horsepower engine, the fuel consumption would increase from 8.7 gallons per hour to 10.3 gallons per hour, resulting in an increased operating expense of nearly $2 per hour.
Pump engines should be tuned up at the beginning of each irrigation season to ensure efficient performance. Air and fuel filters should be changed at manufacturers' recommended intervals.
Electric Motors. A buildup of dirt or oil, obstruction of cooling vents, worn or dragging motor bearings, and voltage surges caused by lightning can cause electric motors to overheat. Overheating often leads to shorted wires in the winding and is the most common cause of low motor efficiency. Voltage surges can also cause damage to or misalignment of phases in three-phase motors, resulting in low motor efficiency. Misaligned shafts between motor and pump and over tightened packing glands or seals can also reduce efficiency. Low efficiency caused by extended use (wear) can sometimes be improved by replacing the commutator (brushes) or having the motor rewound. In the case of small motors (20 to 25 horsepower or less) it is usually more practical to replace the entire motor. Electric motors should be protected from rain and direct sunlight.
Matching System Components. Often, irrigation systems are altered from their original design, resulting in mismatching of components. Alterations such as adding or deleting sprinklers or laterals are often made without making corresponding adjustments to the pumping plant. A change in the depth to water, particularly in some deep wells where the static head has declined, can alter the pumping conditions enough that the pump no longer operates in the recommended efficiency range.
In some cases, the pump can be adjusted to resume operation within the recommended range. On turbine pumps the bowls can be adjusted or impellers trimmed. If wear is excessive, bowls and impellers should be replaced. If an internal combustion engine is used, the system can some- times be adjusted by changing the operating speed. Other cases may require more costly adjustments, such as replacing the electric drive motor or the entire pump.
Minimizing Pressure Losses. Reduced irrigation efficiency can also result from poor maintenance and from wear of system components, leading to excessive pressure losses. With surface-water sources, intake hoses should be checked routinely for clogging and for air leaks or partial collapses of the suction hose. Couplers should be checked for leaks and adjusted or replaced when necessary. Check for misalignment of the rubber seal in quick-connect couplers. Sprinkler nozzle wear is a common cause of poor water use efficiency. Worn nozzles apply more water at lower pressure, leading to excessive water use and poor application uniformity. With most sprinklers it is easy to replace nozzles and other mechanical parts.
Using undersized pipe, especially for mainlines, can significantly reduce energy efficiency. This problem is common when the pumping plant has been adjusted or modified to increase system capacity. For a given flow rate, friction loss and thus pumping cost decrease as pipe size increases (Figure 6). For example, consider a pumping plant modified to increase system capacity by 50 percent from 800 to 1,200 gallons per minute (GPM). The typical mainline pipe for an 800-GPM system is 8 inches in diameter. But when the flow rate is increased to 1,200 GPM, the fuel cost required to overcome the additional friction losses in 2,000 feet of 8-inch mainline pipe compared to 10-inch pipe is nearly $1 per hour. In this case, the long-term energy savings should be weighed against the cost of installing larger pipe.
Adjusting or replacing system components can often improve overall efficiency. These adjustments are usually fairly inexpensive, and in many cases the cost is justifiable. In some cases, however, water- and energy-use efficiencies may remain relatively low. For example, older pumps, even when properly adjusted, are not as efficient as pumps available today. High-pressure systems are not as energy efficient as low-pressure systems. Therefore, it is sometimes necessary to replace costly system components to gain efficiency.
Managing for Water and Energy Conservation
Converting to a Low-Pressure System
Reducing the pressure requirements of an irrigation system reduces the amount of energy it consumes. Converting an agricultural irrigation system from high pressure to low pressure could reduce energy usage by approximately 50 percent. (This percentage is based on a typical high-pressure system requiring 130 to 160 pounds per square inch (PSI) at the pump compared to a low-pressure system requiring only 65 to 80 PSI.)
Some systems can be converted to low pressure simply by replacing existing sprinklers with low-pressure sprinklers designed to reduce operating pressure by 25 to 50 percent. Low-pressure systems typically have high instantaneous application rates and are therefore most appropriate for use on sandy soils, which have a high infiltration rate.
Sprinkler nozzles are designed to operate within a narrow range of pressures. Correct nozzle pressure is necessary to ensure uniform water application. Thus, converting to low-pressure nozzles also requires adjusting the pump pressure. Pump replacement, a more expensive alternative, may be necessary in some cases. Be aware that reducing operating pressure may lead to one or more of the following problems:
- sprinklers may not throw water as far (reduced wetted diameter);
- droplet size may increase; and
- pattern shapes of individual sprinklers may change.
These changes may cause:
- application rates on moving sprinklers to be higher;
- the uniformity on fixed-spacing sprinklers to decrease;
- surface runoff to increase.
Increased droplet size can cause soil surface compaction because the impact energy of larger drops is greater.
Water Management
In striving for efficient use of water and energy, managing an irrigation system properly is as important as selecting the right system. The greatest efficiency is achieved when just the right amount of water is applied at just the right time. The amount of water to apply and when to irrigate are daily management decisions that are influenced by the type of system selected, soil properties, crop, and prevailing climatic conditions, including both temperature and rainfall.
Irrigation scheduling is the process of evaluating these factors and determining when to irrigate and how much water to apply. The effect of soil, water, and crop factors on irrigation scheduling is discussed in Extension publication AG-452-1, Soil, Water, and Crop Characteristics Important to Irrigation Scheduling.
Irrigation scheduling strategies are discussed in Extension publication AG-452-4, Irrigation Scheduling to Improve Water- and Energy-Use Efficiencies.
Water Conservation
Management practices that conserve water usually conserve energy as well. Irrigation scheduling is one way to save water. Practices such as minimum tillage and residue management can retard surface flow, minimizing surface runoff and increasing infiltration so that less water must be supplied by irrigation. Recovering and re-using surface runoff does not reduce energy use but conserves water. In soils that develop compacted layers, deep tillage can be used to increase infiltration and expose a larger portion of the soil reservoir to crop roots. Some of the additional soil-water storage capacity will be replenished by rainfall, reducing the need for irrigation. Extension publication AG-353, Subsurface Compaction and Subsoiling in North Carolina, discusses conditions where deep tillage can be used to advantage. Other water-conserving strategies are currently being studied. They include developing drought-tolerant plant varieties, curtailing vegetative growth (a practice already used in peanut and cotton production), and chemically restricting the evapotranspiration rate. The production cost of keeping plants in a slightly stressed condition is also being evaluated.
Electric Load Management
Electrically driven irrigation systems consume a large amount of electrical power during June, July, and August. The electric power supplier must provide generating facilities and transmission lines capable of meeting the peak demand. Monthly electric bills consist of charges for the amount of electricity used, a charge for maintenance of the generating facility and transmission lines, and a peak demand charge. The peak demand charge for the month is based on the highest power consumption (demand) during any single hour (sometimes quarter hour). This amount is billed every month, even during the months when irrigation pumps are not operating.
There are a number ways of to minimize peak electrical demands. Irrigators can voluntarily schedule irrigation at night during nonpeak periods (typically 10 p.m. to 10 a.m.), thus reducing power consumption during the peak demand period. Some power companies offer financial incentives to customers who allow the company to interrupt power to the pumping unit during high demand periods using a remote control system. See your power company agricultural representatives for information on available programs. As discussed earlier, some systems can be redesigned to reduce pressure and discharge. Improving pumping plant efficiency will also reduce power usage. Procedures for testing pumping plant performance are discussed in Extension publication AG-452-6, Pumping Plant Performance Evaluation. Each alternative for conserving energy has a cost and will reduce peak demand by a different amount.
One option that requires no new equipment is to take advantage of time-of-use rates offered by electric power suppliers. These rates encourage customers to avoid using electrical power during the hours of peak demand (usually from 10 a.m. to 10 p.m.). To take advantage of off-peak rates, you need to know the capacity of your irrigation system and the time it takes to deliver the amount of water needed during periods of high moisture stress. To provide adequate amounts of water during off-peak times, it may be necessary to purchase additional equipment to pump greater quantities of water during the off-peak hours. Planned use of the water stored in the crop root zone is the key to effective off-peak irrigation scheduling. Soil moisture monitoring is a necessary safeguard to assure that soil moisture levels are adequate.
Know Your Irrigation System
Irrigation can be very cost effective. It can lead to greater yields, improved crop quality, improved management capabilities, and perhaps fewer production worries. But selecting the proper combinations of system components and managing the system for greatest efficiency can be complicated. An energy-efficient system is one that has been designed for a particular layout. It must have a pump properly matched to the power unit, the correct pipe sizes, and the proper pressure and water distribution uniformities. Efficiency is achieved by selecting a water- and energy-efficient system and then properly operating, maintaining, and managing it.
As energy costs increase, efficient irrigation systems can mean more money in your pocket. Consider having your system checked periodically to ensure that it is operating at peak performance. Your irrigation dealer can often recognize components that have become inefficient as the system ages. In addition, you’re county Cooperative Extension Service and Soil Conservation Service offices are available to help. Their staff members have received training on irrigation design and can recommend management strategies for efficient, long-term operation of your system.
Words to Know
Term | Definition |
---|---|
Gross Water Applied |
Total water pumped divided by the wetted area during one irrigation, usually expressed in inches per acre. One inch of irrigation water applied to 1 acre is equivalent to about 27,000 gallons. |
Net Water Applied |
The amount of walter pumped that infiltrates the soll and remains in the root zone for use by the crop. It does not include the amount of water lost by wind drift or evaporation, surface runoff, or deep percolation below the root zone. |
Water-Use Efficiency (WUE) |
The percentage of water applied that can be used by the crop-that is, the net water applied divided by gross water applied times 100. |
Term | Definition |
---|---|
Static Head |
The vertical distance that water must be lifted from the water source to the highest elevation in the system. |
Dynamic Head |
The sum of friction losses in pipe lines and fittings plus the pressure drop at sprinklers or emitters.
|
Total Dynamic Head (TDH) |
The "head" or pressure needed at the pump to move the required volume of water through the system and discharge it at the recommended nozzle pressure. It is the total of all head losses. |
Water Horsepower |
The power required to deliver the desired flow rate at the desired discharge pressure. |
Fuel Consumption |
The rate at which energy is consumed to deliver the required water horsepower. It is measured in gallons per hour (gal/hr) for internal combustion engines and in kilowatt-hours (kWh) for electric motors. |
Energy Efficiency | Water horsepower delivered divided by the fuel consumption. |
Energy-Use Efficiency or Performance Rating |
Energy efficiency divided by the performance standard. |
Publication date: Jan. 1, 1996
Reviewed/Revised: July 26, 2024
AG-452-05
N.C. Cooperative Extension prohibits discrimination and harassment regardless of age, color, disability, family and marital status, gender identity, national origin, political beliefs, race, religion, sex (including pregnancy), sexual orientation and veteran status.