A guide for turkey producers, integrator personnel, ventilation professionals, Extension personnel, students, and researchers
North Carolina is the second largest turkey-producing state in the U.S. after Minnesota, producing 32 million birds in 2011. Aside from disease and feed cost, heat stress is the most significant management challenge facing the N.C. turkey industry. Since this review covers ventilation for cooling of heavy strains of turkeys during the growing period after brooding, minimum ventilation will not be discussed.
North Carolina summers have become warmer. For example, average air temperature during the summer (May–September) in Clinton, the county seat of Sampson County, which is the largest turkey-producing county in N.C., averaged 1.5°F higher during 2007–2012 than the 30-year (1971–2000) average of 75.2°F. During July 2012 (hottest month on record), 342,500 turkeys died of heat stress in a 10-county region in eastern North Carolina (James Parsons, personal communication, 20 August 2012). Additionally, the following turkey-related factors can increase heat stress in today’s turkey.
Body weight: Turkeys are being marketed at a heavier weight. An average N.C. turkey weighed 35.4 lb in 2011, up from 25.2 lb in 2000 (NCDACS, 2012). A bigger bird takes longer to cool down because it has less surface area per unit weight and a deeper core than a smaller bird; thus, larger birds are at a greater risk of heat stress. There are reports that during July 2012, turkeys that survived the daytime heat perished at night because of warm and muggy conditions.
Lean genetic lines and high-energy diets: Lean genetic lines and high-energy diets have a synergistic effect on heat production. Being faster growing, modern turkeys are fed a higher-energy diet than the older genetic lines. Being leaner, modern turkeys have higher metabolic rates and heat production than the older turkeys. Chepete and Xin (2002) reported that the 1992–1998 line of turkeys produced more heat than the 1974–1977 line; a 45-lb turkey from 1992–1998 produced 170% more heat than the same size of bird from the 1974–1977 line (Figure 1). Havenstein et al. (2007) reported that energy content in the 2003 diet was consistently higher than the 1966 diet; the 2003 diet for 17 weeks or older turkeys had 18% higher energy content than the 1966 diet. Havenstein et al. (2007) also reported that during hot and humid weather, turkeys older than 9–10 weeks fed the 1966 low-energy/high-protein diet generally performed better than those fed the 2003 high-energy/low-protein diet. While data are not available, the current genetic line could produce more heat than the 1992–1998 line studied by Chepete and Xin (2002).
There is a need to re-examine the way we ventilate to cool grower turkeys. But first, let’s discuss psychrometrics and related concepts.
Psychrometrics and Related Concepts
Psychrometrics is the study of the physical and energy-related properties of moist air; its knowledge improves our understanding of ventilation and cooling. If we know two properties of moist air (such as dry-bulb and wet-bulb temperatures), all other properties can be calculated with a psychrometric chart or calculator. There are many free online psychrometric calculators. Munters Corp. also has a free psychrometric app, PsychroAppTM for the iPhone, iPod touch, or iPad. Because we have not tested these tools, we cannot guarantee their accuracies. Although a detailed discussion of psychrometrics is beyond the scope of this publication, we present here some useful concepts.
Dry-bulb temperature: This is the temperature measured with an ordinary thermometer or temperature sensor, which we usually just call temperature.
Wet-bulb temperature: When the bulb of a thermometer is wrapped with a moist cloth and air is drawn over it, the thermometer will read lower than the dry-bulb temperature because heat from the surrounding air will cause the water to evaporate and the thermometer bulb to cool down. This temperature, known as the wet-bulb temperature, will be lower in the drier, desert climate of Arizona than in North Carolina.
Relative humidity (RH): Expressed as a percentage, RH is the ratio of the amount of water vapor in the air at a certain temperature to the maximum amount of water vapor that the air can hold at that temperature without condensing. Moisture-holding capacity of air nearly doubles with every 20°F rise in temperature. As RH increases, people become uncomfortable because the sweat does not evaporate as rapidly off of their bodies. In Arizona, RH will be generally much lower than in North Carolina, which is more humid.
British thermal unit (BTU): This is a commonly used unit of heat energy. It is the amount of energy required to raise the temperature of 1 lb. of water by 1°F. For reference, 1 gallon of propane has 92,000 BTU of heat energy.
Sensible heat and latent heat: Heat energy that causes the temperature to increase without a change of state (say, from ice to water) is sensible heat. While 1 BTU is needed to raise the temperature of 1 lb of water by 1°F, for 1 lb of ice, we need only 0.56 BTU.
Latent heat is that heat energy that causes a change in state (such as from liquid to vapor) without a change in temperature. When water at 80°F evaporates, 1,048 BTU of heat (latent heat of vaporization) is transferred into the air per lb of water evaporated without a change in temperature. If water vapor were to condense back into liquid at 80°F, 1,048 BTU/lb of heat would be released back into the liquid (latent heat of condensation). At the boiling point of water (212°F), latent heat of vaporization is only 970 BTU/lb of water. Similarly, at 32°F, when water freezes or ice melts without change in temperature, 144 BTU/lb of energy is released (latent heat of freezing) or absorbed (latent heat of melting).
Because water needs more energy to heat up than dry air and a large amount of heat is released or absorbed when water changes phase, despite water vapor being a small fraction (about 2% by mass at 80°F in saturated air), it accounts for a disproportionately large fraction of the energy content of air. In saturated air at 80°F, 56% of the energy is due to water vapor and only 44% due to the dry air fraction.
Turkeys produce both sensible heat and latent heat. The purpose of the ventilation system is to remove all the sensible or latent heat produced by the bird; otherwise, the turkey’s body temperature will rise and it will die. Therefore, information on sensible heat loss is required to calculate hot-weather ventilation rates, which are adequate for removing all the moisture produced. Latent heat production information is required for cold-weather ventilation rate calculation.
Enthalpy: Enthalpy is the heat energy content of the air (BTU/lb-dry air) and is read from the psychrometric chart. More heat can be removed from a barn if the fresh air has lower enthalpy. Air at a temperature of 80°F and RH of 40% will have an enthalpy of 29 BTU/ lb dry air. However, if the air has a temperature of 80°F and RH of 80%, its enthalpy will be 39 BTU/lb dry air. Since water vapor can store more energy than air, the more humid air holds more energy and removes less energy.
One pound of dry air at 80°F and 40% RH occupies 13.8 ft3 of space (from the psychrometric chart); therefore, a 48-in. fan moving 20,000 cfm will pull in 1,449 lb/min of dry air. The more humid air (80% RH) will bring in 869,400 BTU/hour more heat than the 40% RH air, which is the same as burning 9 gallons of propane every hour! This clearly shows the importance of RH.
Efficiency of evaporative cooling system: This term is used to calculate the effectiveness of evaporative cooling systems (evaporative cool cell pads, fogging, and misting) used in turkey houses. The efficiency (Eff, %) of an evaporative cooling system is:
Eff=T−TinT−Twb×100. [1]
where T and Twb are outdoor dry-bulb and wet-bulb temperatures and Tin is the inside dry-bulb temperature after evaporative cooling. Let’s assume T is 100°F, Twb is 65°F, and Tin is 74°F. Hence, the cooling efficiency is 75%.
In theory, if the air is very hot and dry and the system design is perfect, the air temperature could be reduced to its wet-bulb value. In North Carolina, for design, we assume that evaporative cool cell pads are 75% efficient and foggers have efficiencies of 25% to 35%.
Heat Loss Mechanisms in Turkeys
Sensible heat is transferred through conduction, convection, and radiation. Conduction occurs when two bodies with different temperatures touch one another and heat moves from the warmer body to the colder body. Convection happens when moving fluid transfers heat to a colder body or transports heat away from a warmer body. Radiation occurs when a colder body receives heat energy from a warmer body in the form of electromagnetic waves that can travel through air or vacuum, as in the sun warming up the earth. For example, while a turkey with a body surface temperature of 88°F will receive heat from a hot, uninsulated roof at 120°F during daytime, at night as the roof temperature decreases to 70°F, the roof will receive heat from the turkey.
Latent heat loss occurs mainly through evaporation or sweating in humans. However, turkeys cannot sweat and lose latent heat through panting and fecal excretion (including heat stress-induced diarrhea, also referred to as “flushing”). As temperature increases, turkeys increasingly use compound ventilation, a combination of breathing (high frequency, low tidal volume) with panting (lower frequency, higher tidal volume) to maintain body temperature (Brown-Brandl et al., 1997a).
Heat exchange through conduction, convection, radiation, and evaporation are interrelated and will depend on environmental conditions. As temperature increases, due to a smaller temperature difference between the turkey’s body surface and the surrounding air, sensible heat loss decreases (Table 1). Similarly, as RH increases, the turkey’s ability to lose latent heat decreases (Table 1).
Sex | Weight, lb | Temperature, F | RH, % | As percent of total heat loss1 | |
---|---|---|---|---|---|
Sensible heat | Latent heat | ||||
Male | 19.7 | 65 | 76 | 69 | 31 |
Female | 9.6 | 64 | 85 | 72 | 28 |
Male | 19.7 | 77 | 52 | 56 | 44 |
Female | 9.6 | 79 | 63 | 28 | 72 |
1Average of light and dark periods ↲
Thermal Regulation and Environmental Stresses in Turkeys
Except when very young, being homeotherms, turkeys can maintain their body temperatures within a narrow range of ambient air temperature without much effort; the turkey performs best in this zone of thermal comfort (MWPS-1, 1983). However, the zone of thermal comfort depends on several different factors and changes with age. Whereas day-old poults prefer a temperature of 90°F to 92°F, 40-lb toms prefer a much lower temperature range of 65°F to 67°F. Once the ambient temperature increases above (or decreases below) the zone of thermal comfort, the turkey uses various behaviors (such as standing up to lose heat) and autonomic (panting) responses to decrease or increase metabolic heat production (and/or heat losses) to maintain body temperature. Ventilation and cooling must be provided to prevent the barn temperature from approaching the upper critical temperature for the turkey when the body temperature begins to increase, which may result in death.
Temperature and RH both affect the turkey’s well being, and they affect toms and hens in slightly different ways. Researchers have evaluated the combined effects of temperature and wet-bulb temperature (as a surrogate for RH) on physiological parameters (such as heart rate), heat production, or performance. Brown-Brandl et al. (1997b) developed the temperature-humidity index (THItom) for 6- to 20-week toms (equation [2] for 15-week toms presented below). Xin et al. (1992) developed THIhen for 15-16 week hen turkeys (equation [3]).
THItom=0.53T+0.47Twb [2]
THIhen=0.74T+0.26Twb [3]
In both equations [2] and [3], T and Twb are dry-bulb and wet-bulb temperatures (ºC), respectively. At 15–16 weeks of age, the hens seem to be much more affected by temperature (equation [3]) than toms are (equation [2]). Being taller and having a longer snood, larger dewlap, and major caruncles helped the tom dissipate heat more effectively than the hen. Table 1 also shows that in the higher temperature range, at about comparable temperature and 11% higher RH, toms lost more heat as sensible heat than hens did. However, during the July 2012 heat wave, more fully grown toms than hens succumbed to heat stress, probably because the much-larger tom with a deeper core and lower surface area per unit mass cooled down slower than the hen.
The THI equations presented above could be used to improve animal performance and welfare in naturally ventilated barns, but an increasing number of turkey grow-out barns are tunnel ventilated, where high air velocities also contribute to cooling. Tao and Xin (2003) developed a temperature, humidity, and air velocity index (THVI) for broilers. These indexes are based on short-term observations of acute effects. But the bigger concern may be the impact of prolonged (8–10 hours) and repeated sub-lethal hot and humid conditions on animal performance. A THVI that looks at chronic effects on turkey performance probably may be more useful.
Turkeys handle environmental stresses better than chickens (Brown-Brandl et al., 1997a; Yahav, 2000). Although hot weather increased panting and caused respiratory alkalosis, reducing broiler growth rates, it did not affect turkeys as much (Yahav et al., 1995). There are several reasons for this. Because the chicken has been more aggressively selected for increased body weight than the turkey, the chicken has a relatively smaller cardio-pulmonary system, which reduces its ability to handle heat stress. Being taller, a turkey will have more air circulation beneath its body. A turkey can dissipate a disproportionately larger amount of heat than a broiler through its bare head and neck regions. As is clear from Figure 2, the head region, which is 15°F warmer than the feather-covered body, is much more effective at losing heat. Finally, a turkey’s compound ventilation system seems to be quite effective in reducing heat build-up.
Turkey Barn Ventilating and Cooling Systems
The purpose of hot-weather ventilation is to maintain acceptable temperatures inside the barn, and this is achieved by removing all the heat that is produced (from animals and equipment, and through solar heat gain). Earlier, the objective of hot weather ventilation was to keep the barn temperature within 3°F to 5°F of ambient temperature. The older line of turkeys produced less heat and because of technology constraints (such as less powerful controllers), trying to maintain inside temperatures slightly above ambient temperature made sense. However, in the 21st century, because of better technology and greater need for cooling, hot–weather ventilation and cooling should be optimized for animal performance and welfare.
When designing a hot-weather ventilation system, we consider three aspects, namely (a) airflow rate, (b) temperature of the fresh air, and (c) air speed. If the fresh-air temperature is below the desired temperature of the barn, moving enough air will remove enough heat to keep the animals comfortable. However, if the air temperature is higher, we must either cool the air (mostly through evaporative cooling), create a wind–chill effect using high air speeds, or do both. Simply moving excessive amounts of air through the barn without adequate cooling will not always keep the birds comfortable; for example, if the air temperature is very high, high airflow rates will cause the birds to overheat. Similarly, excessive evaporative cooling with inadequate airflow rate will make the house humid and the litter wet.
There are three types of hot weather ventilation systems: naturally ventilated, sidewall (or cross-ventilation), and tunnel systems, and it is in the tunnel system that all three hot-weather ventilation aspects can be best balanced. Cooling is provided with misting/fogging systems in naturally or sidewall-ventilated barns, while tunnel barns can use evaporative pad cooling or misting/fogging. All three types of ventilation systems are discussed here.
Naturally ventilated barns: Naturally ventilated barns rely on natural air movement through curtains and large, sliding, screened doors to bring in fresh air. These barns also have circulation fans. Although some grow-out barns still have manually operated curtains, most barns have curtains that are controlled by thermostats. Because a naturally ventilated barn relies on wind and buoyancy forces to provide air exchange, a vaulted roof with ridge or chimney openings is required. The underside of the roof should be insulated with a 1-inch thick polystyrene foam board to reduce radiational heat gain and eliminate condensate dripping down from the roof onto the birds in cool and cold weather. An uninsulated metal roof can get very hot in summer and increase bird discomfort (Figure 3).
Nowadays, most naturally ventilated barns have a hybrid ventilation system—in winter, they use ventilation fans on the north side and inlets (on both sides) while in warm weather, curtains are lowered to provide greater air exchange, and the system reverts to natural ventilation. Such a hybrid system generally has poor air distribution because it is leaky. Two 36-in. fans with typical airflow rate of 10,000 cfm per fan can provide minimum ventilation for 5,000 40-lb toms.
Circulation fans in naturally ventilated barns create some air movement, but they contribute little to air exchange. The total capacity (cfm) of circulation fans installed in naturally ventilated barns depends on the turkey integrator but can range from 75% to 100% of the capacity of tunnel-ventilated barns. Typically, 36- to 48-in. circulation fans are placed along the long axis of the barn. Fresh air is brought in and stale air exhausted through the screened doors at opposite ends. A 48-in. circulation fan will cover a total floor area of 1200 ft2 (60 ft × 20 ft) while a 36-in. fan will cover 675 ft2 (45 ft × 15 ft). Up to seven 48-in. or nine 36-in. fans would be needed to cover a 400-ft-long barn, but this arrangement will provide cooling mainly in the middle, leading to crowding. Midwest Plan Service (MWPS) (MWPS-32, 1990) recommends angling the fans at about 15° sideways so that the air moves in a “rotational racetrack” pattern through the barn (Figure 4). Because the fan spacing can be increased up to 25 fan diameters for the racetrack design (MWPS-32, 1990), only 10-12 36 in. fans would be needed to cover the barn.
The height of the circulation fan above the floor and its tilt angle are important in ensuring adequate air speed over the birds. A clearance greater than 40 in. between the fan and the floor reduces the fan’s effectiveness. Bottcher et al. (1995) recommended that fans be tilted 10º to 20º downward (as measured at the shaft) from the horizontal. While tilting at 10º threw the air farther, a 20º tilt provided greater lateral coverage (Bottcher et al., 1995). We measured an air speed of 400 ft/min, 36 in. above the floor, 40 ft in front of a fan that was angled downward but when the fan was not angled downward, it was less than 200 ft/min. Angling the fan upward is undesirable because it will pull some of the heat that has accumulated at the top toward the birds.
During hot weather and with large birds, evaporative cooling (fogging or misting) will be required to prevent catastrophic heat build-up. In fogging, pressures between 200 to 1,000 psi produce very fine droplets and when these droplets evaporate in the air, they reduce the temperature of the air while increasing its RH. A gallon of evaporated water will convert about 73,000 BTU of sensible heat into latent heat. Bottcher and Czarick (1997) recommended 1 gal/hr from every 1,000 cfm for tunnel ventilation, and this value could also be used for natural ventilation. Under summer design conditions for Raleigh (92°F dry-bulb and 46% RH, MWPS-1, 1987), using psychrometrics, 1 gal/hr of fogging per 1,000 cfm of ventilation can reduce the temperature by 10°F if all water is evaporated. But with 200 psi, only a fraction of the water is evaporated and efficiencies range between 25% to 35% (equation [1]), which would result in a temperature drop of 6°F under Raleigh design conditions. However, even when a large fraction of the water is deposited on the birds and litter, it will provide additional cooling, as discussed later. With higher operating pressures or in drier climates, higher water flow rates could be used. Typically, nozzle flow rates range from 1 to 2 gal/hr. Foggers are operated by a thermostat; at lower temperatures, they are operated intermittently but if temperatures continue to rise, they are used continuously. Placing fogger nozzles in front of the circulation fans or fans pushing air into the barn will allow the droplets to be dispersed widely and evaporate better, providing more cooling. Because fogging requires higher pressures than misting (120 to 140 psi), more expensive equipment and greater maintenance are required; therefore, turkey producers generally prefer misting.
In misting, water pressures are 120 to 140 psi and nozzles have flow rates of 3–4 gal/hr. Misting rates of 1 gal/hr for every 1,000 cfm of circulation fan capacity, or 7 to 10 gal/hr nozzles with a 36-in. fan, seem to be reasonable. Nozzles mounted directly on the fans are preferable to mounting these nozzles separately, but be careful to avoid caking on the fan. Misters are also operated by thermostat with intermittent operation at lower temperature and continuous operation at higher temperature. Because of lower pressure than fogging, water droplets are larger and end up on the birds and litter. Evaporation of droplets landing on the bare surfaces of the head and neck of the turkey probably provides considerable cooling. However, there is no information in the literature regarding the efficiency of misting in naturally ventilated barns. Compared with fogging, misting may create more wet litter problems.
Sidewall-ventilated barns: In these barns, fans are set just inside the open sidewall either along one side or alternating along both sidewalls (Figure 5). The air is pushed into the barn by the fans and exhausted through the curtain and end-door openings. Ventilation professionals have been designing tunnel ventilation systems with evaporative cooling in eastern N.C. and S.C. using rates of 1 to 1.1 cfm/lb or 12-14 cfm/ ft2 of barn area based on current stocking densities. Using a ventilation rate of 1 cfm/lb, a 40 ft × 500 ft barn with 5,000 45-lb toms would need 225,000 cfm of ventilation provided by 10–11 48-in. or 20–22 36-in. fans. However, even with this high ventilation rate, higher than that for a tunnel house of the same size (discussed later), the entire floor area will not covered. The rule of thumb is that a fan pushing air into the barn will move air 15 times the fan diameter in front and 2.5 times the fan diameter on each side (for a total of 5 fan diameters along the width). Therefore, 22 36-in. fans would cover only 330 ft of the 500-ft long house, whereas the 11 48-in. fans would cover only 220 ft! To cover the entire length of the house, 33 36-in. or 25 48-in. fans would be needed, which would be prohibitively expensive. Instead of increasing the number of fans, angling the 48-in fans sideways at about 40º will greatly improve the coverage in the barn (Xin et al., 1994). Unlike the minimum ventilation fans, mild and summer ventilation fans should be installed on the south wall and angled toward the east to take advantage of the predominant wind direction, which is south to southwest.
On very hot days, evaporative cooling will be needed. Czarick recommended 1 gal/hr from every 1,000 cfm for tunnel ventilation, and this value may also apply to sidewall ventilation. Mounting the nozzles directly on the fan or close to it with the spray slightly angled into the airstream will allow the droplets to be dispersed widely, reducing wet spots. Although MWPS (MWPS-34, 1990) recommends reducing the maximum ventilation rate by 40% when evaporative cooling is provided, this will result in a much greater portion of the house receiving no airflow than if no evaporative cooling is provided.
Tunnel-ventilated barns: Tunnel-ventilated turkey grow-out barns are becoming more popular in North Carolina. In these barns, fresh air is brought in through large openings at one end of the barn and exhausted through the other end with fans (Figure 6). The resulting high air speeds (600 ft/min or higher) provide considerable wind chill effect. These air speeds are average values obtained by dividing the total ventilation rate (cfm) by the cross-sectional area of the barn and are not the speeds at bird height.
Tunnel ventilation is more appropriate for barns that have high length/width ratios, preferably, 10/1 or higher. For example, there are two barns 50 ft × 400 ft and 40 ft × 500 ft and both have drop ceilings the same height (say, 8 ft) from the floor. Both barns have the same area and hold the same number of birds and would therefore have the same ventilation rate (say, 200,000 cfm). However, compared to the 50 ft × 400 ft which has a cross-sectional area of 400 ft2 (8 ft × 50 ft) and an average air speed of 500 ft/min (200,000/400), the 40 ft × 500 ft barn, with a cross-sectional area of 320 ft2 (8 ft × 40 ft), would have an average air speed of 625 ft/min (200,000/320)! Therefore, to convert short barns into tunnel ventilation, you have to install excess fan capacity to get the high air speeds required for adequate wind chill. For 300- to 350-ft barns, a target air speed of 500 ft/min is more realistic.
Unlike broilers, there are no published data on air speed effect on turkey performance, but high air speeds reduce heat stress in turkeys (Figure 7). Hence, we need to investigate the effects of high air speeds (up to 800 ft/min?) not just on turkey performance but also on economics, as more fans and electrical energy will be required. Despite additional electricity costs, broilers receiving 24 hr of 550 ft/min air speed provided $129 more in returns than those that received 12 hr of 550 ft/min and 12 hr of 325 ft/min (Dozier et al., 2006). Sustained cooling of large turkeys through the night might result in birds eating more during the cooler part of the day to gain more weight.
We do not have recently published ventilation data for turkeys. The MWPS recommends 0.8 cfm/lb for growers (MWPS-32, 1990), which may be inadequate for current conditions. As mentioned earlier, tunnel-ventilation systems with evaporative cooling in eastern N.C. and S.C. are being designed using rates of 1 to 1.1 cfm/lb or 12-14 cfm/ft2 of barn area based on current stocking densities. Based on the sensible heat production data for the 1992–1998 turkeys (Table 1 and Figure 1), about 0.9 cfm/lb would be required, assuming that heat losses and gains from other sources and sinks are negligible compared to the heat produced by the birds. Because the current line of turkeys will surely produce more heat than the 1992– 1998 line of turkeys (Figure 1), and we desire an air speed of about 600 ft/ min, the ventilation rate of 1 to 1.1 cfm/lb used by ventilation professionals may be more appropriate. In a 40 ft × 500 ft barn with a cross-sectional of 320 ft2, 5,000 40-lb toms would require about 180,000 cfm, which would produce an air speed of 560 ft/min if a design rate of 0.9 cfm/lb of bird marketed is used. If a ventilation rate of 1 cfm/lb is used, for the same house, the ventilation rate required is 200,000 cfm and the air speed is a more desirable 625 ft/min. In a 50 ft × 400 ft barn (cross-sectional area of 400 ft2), even with a ventilation rate of 1.1 cfm/lb, the air speed will only be 550 ft/min.
When ambient air is above 95°F, running hot air over the birds can actually increase heat stress. In tunnel barns, the fan end may be warmer than the inlet end by as much as 6ºF because as air travels through the house, it picks up heat. Therefore, tunnel-ventilated turkey grow-out barns need evaporative cooling. However, evaporative cooling should be used only when the RH is below 70% (usually between 10 a.m. and 6:00 p.m. in N.C. during summer). In humid weather, air cannot absorb much more additional water vapor and the temperature drop may be too small to justify running it. Operating the evaporative cooling system too early in the staging of the tunnel-ventilation system will also result in wet litter because low air speeds in the house will not have as much energy to disperse the water droplets widely and low temperature (generally, high humidity) will reduce evaporation. Therefore, it is important to match the water application rate of the evaporative cooling system with the airflow rate.
The most effective evaporative cooling system is the recirculating pad. In this system, as warm air is pulled through a wet pad, sensible heat in the air is transferred to the water, As evaporation occurs, the air is cooled even though its RH increases. Such systems are more effective in the drier parts of the U.S., but even in North Carolina, during the hottest part of the day when RH is low, they can reduce temperature by more than 20°F. Bottcher and Czarick (1997) reported system efficiency (equation [1]) of up to 89%, though for design we use 75%. There is no research on turkeys, but Xin et al. (1994) reported that in broilers, the pad system provided greater cooling than fogging.
Sizing the pad area in relation to the maximum ventilating rate is very important. For a 6-in. thick cellulose pad, the generally recommended pad airflow rate is 350 cfm per square foot of pad (or 350 ft/min pad velocity) for a static pressure drop of about 0.1 to 0.15 in. water column, a range commonly used in sizing fan capacity in livestock barns. So, for a maximum ventilation rate of 200,000 cfm, about 570 ft2 (200,000/350) of pad area is needed. With undersized pad area, there may be excessive pad velocity resulting in greater pressure drop, which will reduce fan airflow rate, which will reduce air speed in the house and provide less cooling. Optimizing the pad area will reduce pressure drop, increasing both air speeds in the tunnel house and temperature drop at the pad, improving bird cooling. Proper pad area will also increase fan efficiency, resulting in more air being moved through the house per unit of electricity used. Pad velocity and air speed inside the house are different, though they are related.
Another type of evaporative cool cell pad is a fogging pad system in which water is sprayed on the pad with nozzles on the outside. It can drop temperature by as much as 13°F (Bottcher and Czarick, 1997), but it is losing ground to the recirculating pad because of lower efficiency and high water losses under windy conditions.
Evaporative cooling can also be provided by the fogger or misting system described earlier. Bottcher et al. (1989) reported an 11°F drop in temperature and an efficiency of 59% when misting 24-lb hen turkeys at a ventilation rate of 7.5 cfm/bird, much lower than desirable tunnel-ventilation rates. Bottcher and Czarick (1997) recommended fogging rates of 1 gal/hr per 1,000 cfm of ventilation capacity. Ten to 15 nozzles (1-gal/hr) are mounted along the width of the house in each line, and the lines are about 15 ft apart near the tunnel air inlet and 25 to 30 ft apart near the middle of the house (Czarick, 2009). No nozzles lines are placed in the last 100 ft of the house to minimize wetting of the fans (Czarick, 2009). These multiples lines of nozzles are set in different timer stages that are progressively triggered if the temperature keeps rising. Running fogger lines along the length of the house as opposed to across the width of the house can cause droplets to coalesce, become large, and deposit on the birds or floor instead of evaporating in the air. Although foggers are used in conjunction with recirculating pads in heavy-broiler houses, we have not seen them being used jointly in turkey barns.
In summary, compared with naturally and sidewall-ventilated barns, tunnel-ventilated barns with evaporative cooling are probably the most effective in reducing heat stress in turkeys in North Carolina because they provide very good air exchange, cooling, and wind chill. Based on experience with broilers, the recirculating pad system is probably the most effective at reducing air temperatures. However, there is a need to ascertain the benefit-cost of tunnel ventilation system with high air speed for turkeys.
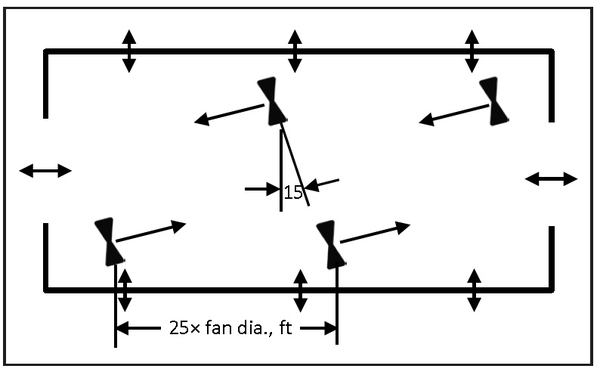
Figure 4. Circulation fans in a “rotational racetrack” pattern. Bidirectional arrows indicate air movement into or out of the barn depending on wind direction. Airflow through the sidewalls occurs through the curtain openings while airflow through the ends occurs through the screen doors. Not to scale.
Based on MWPS-32 (1990).
References
Bottcher, R.W. and M. Czarick, III. 1997. Tunnel Ventilation and Evaporative Cooling for Poultry, AG-554. Raleigh, NC: NC State University Cooperative Extension Service. ↲
Bottcher, R.W., G.R. Baughman, and D.J. Kesler. 1989. Evaporative cooling using pneumatic misting unit. Trans. ASAE 32:671-676. ↲
Bottcher, R.W., J.R. Magura, J.S. Young, and G.R. Baughman. 1995. Effects of tilt angles on airflow for poultry house mixing fans. Appl. Eng. Agric. 11:721-730. ↲
Brown-Brandl, T.M., M.M. Beck, D.D. Schulte, A.M. Parkhurst, and J.A. DeShazer. 1997a. Physiological responses of tom turkeys to temperature and humidity change with age. J. therm. Biol. 22:43-52. ↲
Brown-Brandl, T.M., M.M. Beck, D.D. Schulte, A.M. Parkhurst, and J.A. DeShazer. 1997b. Temperature humidity index for growing tom turkeys. Trans. ASAE 40:203-209. ↲
Chepete, J.H. and H. Xin. 2002. Heat and moisture production of poultry and their housing systems: literature review. ASHRAE Trans. 108:448-466. ↲
Czarick, M., III. 2009. Keeping birds cool during hot weather. Athens, GA: Univ. of Georgia. ↲
Dozier, W.A., III, J.L. Purswell, and S.L. Branton. 2006. Growth responses of male broilers subjected to high air velocity for either twelve or twenty-four hours from thirty-seven to fifty-one days of age. J. App. Poult. Res. 15:362-366. ↲
Havenstein, G.B., P.R. Ferket, J.L. Grimes, M.A. Qureshi, and K.E. Nestor. 2007. Comparison of the performance of 1966- versus 2003-type turkeys when fed representative 196 and 2003 turkey diets: growth rate, livability, and feed conversion. Poult. Sci. 86:232-240. ↲
MWPS-1. 1987. Structures and Environment Handbook, 11th ed. Ames, IA: Midwest Plan Service. ↲
MWPS-32. 1990. Mechanical Ventilating Systems for Livestock Housing, 1st ed. Ames, IA: Midwest Plan Service. ↲
MWPS-34. 1990. Heating, Cooling, and Tempering Air for Livestock Housing, 1st ed. Ames, IA: Midwest Plan Service. ↲
NCDACS. 2012. Turkeys. Raleigh, NC: NC Dept. of Agriculture and Consumer Services. ↲
Ota, H. and E.H. McNally. 1961. Heat and moisture production of Beltsville White turkeys. Poult. Sci. 40:1440 (abstracts). ↲
Tao, X. and H. Xin. 2003. Acute synergistic effects of air temperature, humidity, and velocity on homeostasis of market-size broilers. Trans. ASAE 46:491-497. ↲
Xin, H., I.L. Berry, G.T. Tabler, and T.L. Barton. 1994. Temperature and humidity profiles of broiler houses with experimental conventional and tunnel ventilation systems. Appl. Eng. Agric. 10:535-542. ↲
Yahav, S. 2000. Domestic fowl – strategies to control environmental conditions. Avian Poult. Biol. Rev. 11:81-95. ↲
Yahav, S., S. Goldfeld, I. Plavnik, and S. Hurwirtz. 1995. Physiological responses of chickens and turkeys to relative humidity during exposure to high ambient temperature. J. therm. Biol. 20:245-253. ↲
Publication date: April 1, 2013
Reviewed/Revised: Jan. 16, 2025
AG-775
N.C. Cooperative Extension prohibits discrimination and harassment regardless of age, color, disability, family and marital status, gender identity, national origin, political beliefs, race, religion, sex (including pregnancy), sexual orientation and veteran status.